| |
Project Journal - D14 Engine Rebuild - Clean-up |
Handle: |
YTSupport |
|
Project Name: |
D14 Engine Rebuild - Clean-up |
|
Tractor: |
AC D14 |
|
Started: |
21:10 07/17/17 |
|
Updated: |
19:14 02/13/18 |
|
|
Expand/Contract all Journal Entries Show newest journal entry on top |
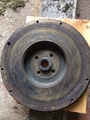 21:34 07/17/17
| 21:34 07/17/17 Flywheel and headWell, today I took the flywheel in for it's grinding. Will be $40. I waited until I verified that I could find the right ring gear. All the folks selling ring gears on the net including us, have the wrong part. Only Agco has the 93 tooth gear that the D-14s used. The 116 tooth is easy to find, but (edit, had to change this after study, I should have listened to our Sales Staff) but applies only to the last 5000 D-14s made, starting not long after mine was made in 59, that was the cutover, identified by the black bar grill. The 116 tooth gear equated to the 12 volt switch over in that same variant. Count your teeth. Ring gear is 93 teeth, starter drive is 9 teeth. If you are lucky enough to have 116 and a 10 tooth starter drive, your parts are reasonable. Agco is quite proud of the 93 tooth gear, the price is double. I did find that I had a spare flywheel, but it was a bit chewed too, and I want this rebuild to feel like new. It is sad because I wanted all parts to come from YT.
Flywheel will be ready tomorrow, ring gear will be here in a couple of weeks, valve job and head surfacing will be back in a week.
The guy doing the flywheel grind is going to try and save the bushing, but it's possible I'm going to have to find one. Pilot bearings are available for G149s that used them, but I'm concern the bushing may not be.
Tomorrow I'll start cleaning up all the extra parts. I'll be using the pressure washer, a grinder and solvents. I am going to order some paint soon. It's difficult to know the right color with a tractor so close to the cutoff, but the original was Persian #1 in places where fading hadn't occurred and I'm going with that for everything that is effected by this job. Eventually, I'll have to re-restore the rest of the tractor since it's got a nice (but faded) Persian #2 job on it. A shame because it actually looks quite good.
Almost forgot. When I took the flywheel in, the guy said he was not going to take off enough material to justify shimming. I like that. It was in better shape than I thought. | | |
|
| 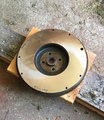 16:35 07/18/17
| 16:35 07/18/17 Flywheel is backI was pleased with how it looked. I took the camshaft in just to check what their opinion was. The fellow that looked it over said the discolorations were not a problem and the shaft is sound. I trust him given that they stand to profit if I had them redo it.
I also got my parts ordered today from the business. Everything turned out to be in stock right here at the warehouse so now I'll just be waiting for the return of the head, surfacing the face of the block, and the new ring gear. | | Comments | kevinthefixer 19:34 07/21/17 | Looks like your machinist is good, he only took off what was necessary, left the rust marks in the spots where they don't matter. I still believe he's wrong on the cam, I wouldn't trust it. What do the lifter faces look like? If they're not pitted you can glue some 150 or 180 grit emery cloth to a flat stone or thick glass and flat-sand them. Works really good on carb gasket mating surfaces too. | YTSupport 11:17 07/22/17 | Kevin, you were on the money on the cam, read the new entry for the 22nd. One lobe is shot. |
|
|
|  | 19:54 07/19/17 BlockGood day, I was able to break loose the oil pickup tube and now can send it off to the shop for hot tanking. The fellow told me on the phone that they will also surface the head to block mating face. I cleaned it up and see no serious problems, they should be able to just touch it a bit and level it without taking off a lot of material which I'd think on a sleeved engine, could be a serious problem. Carrying the block by myself didn't do my back any favors, but I'm happy, everything is falling in line.
Doing this work has got me so excited, I dug my IB out of the blackberries and jacked it up to put blocks under. Doing an IB has always been a fantasy to me. Such a cute little tractor. Unfortunately, the transmission is frozen solid, but that's another journal if I do it. My other D-14 looks like it might be the first candidate since it's all there and in reasonable condition.
Hopefully tomorrow I'll get the head back, possibly pick up all the parts from the warehouse and then I'll be scrambling to clean up all the rest of the parts. Maybe in a week, it will be time to assemble.
I did some study today on assembly oil. I've used 30 SAE before, and this time I was thinking of using assembly lube or even better, just use the HP-4M Honda Moly. I have a case of it left from my old CRF-250X (enduro bike). I'm thinking about using it as the assembly oil and then filling with a good grade SAE 30 that would be better for break-in, then switch to the moly synthetic after 40 or 50 hours. I need to use it and it seems wise to use it in an engine that I care about. | | |
|
|  | 15:08 07/20/17 More on the blockThe block is in for tanking, shaving, and removal of a broken stud they said would be easy for them. I'm good with that as it would probably take me hours. I'll update this later when I have any progress. Today will be cleaning, both parts and the shop.
| | |
|
| 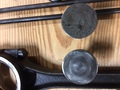 11:11 07/22/17
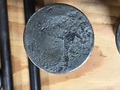 11:11 07/22/17
| 11:11 07/22/17 Cam, lifter, pushrod damageI cleaned up the camshaft and lifters last night. I started with the lifters and on the intake number 1 piston, I found extreme pitting that I'd not noticed. That made me start looking closely at the cam lob and it too was gone. I made an assumption I shouldn't have, had looked over "most" of the lobs and lifters and assumed that if the ones I looked at were perfect, there couldn't be any that were too bad. I was wrong. I have spare lifters so that part is covered since I have a complete spare CE engine, and I even have a spare camshaft (condition unknown since it's still in the other G-149 block). I'm still going to research having this one built-up, ground and hardened because I was really hoping to restore the other D-14. I'm reticent to buy a used one on the internet, too many will sell you something worse than what you already have and we unfortunately do not carry a reground any longer.
I was talking to my brother on this, long time motorcycle, steam engine and lately aircraft mechanic. He felt it had to have sat and developed rust right at that spot to get that bad. During the conversation, I was able to pick his brain on assembly oil since that topic is so contentious on the net, and I've always just used SAE 30. He told me that the regulations require an 80 weight mixed with STP, and that you use a moly grease on the cam (he said he'd give me some since every new camshaft for an aircraft engine comes with a tube and they end up with extras. I think I'll try this this time. He told me that he felt that it's an overblown subject for most engines. If assembly is done in a few days, the assembly oil is not as important, only crucial if you do assemblies and leave things sit, but then, you actually should tear down and re-lubricate everything before lighting it off.
Noted that the push rod on the bad cam lob was badly bent. I didn't see that before so apparently, it was damaged when this engine was fired off after setting for some years. I bought this machine many years ago, but it did look like it might have been setting for years prior to the fellow I bought it from getting it running and putting it up for sale. It was probably at that time the cam busted loose and the push rod bent. Fortunately, I have a pile of good push rods from the BE and CE engines. I went through all of them and ran them across a very flat surface, weeding out those with wows in them and developing a complete set that are straight.
This experience is really driving home how important it is for those of us with many engines sitting around the farm, to keep them in top shape, started frequently and well lubricated. Sitting seems it can sometimes cause as much or more damage than use. This is also a good reason to keep only as many engines around as you can maintain correctly. | | Comments | kevinthefixer 18:43 07/22/17 | Sounds like your bro knows his stuff. Rust damage is exactly what I thought when I saw the pic of the one cam lobe. You used exactly my trick on the pushrods, good job. Recommend you invite your brother over for steak each night you're working on the motor, he's bound to have more tricks that'll save you heartache. Are there still places that will build up a damaged cam? And harden it? How about the bearing journals? BTW the bent pushrods are almost always caused by the valve seizing in the guide, either rust or gas varnish. | YTSupport 20:10 07/23/17 | On my brother, yes, but, big brother has been one step ahead of me all his life in mechanics and electronics, little brother has to have some pride, and of course, no one has to depend on my rebuilds at 5000 feet in the air ;-). But yes, I do call him first when I'm quibbling with myself about any issues. |
|
|
| 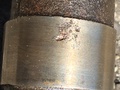 22:25 07/23/17
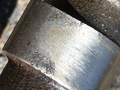 22:25 07/23/17
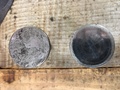 22:25 07/23/17
| 22:25 07/23/17 Another CamshaftI decided to tear down the other D-14 engine and remove the camshaft. The process was a nightmare because the crank pulley was badly stuck on there. I ended up destroying it slowly but did finally get it off. It's an easy part to replace. The second camshaft was not perfect by any means, though significantly better than the other one. It had pitting on two lobes though neither as bad as the first. I am attempting to contact a racing shop to see if they will evaluate both, weld, regrind and harden as necessary. One of the goals is rebuild both engines eventually. There are two shops I've found in the area specializing in cams for hot rods, locomotives and other applications, both say that no job is too small.
I did come out with 8 more lifters that are all in great shape. That means I'll be down one lifter and 3 pushrods to achieve both engines.
I decided to try the ultrasonic cleaner on the parts I was cleaning today, the results are very good so far. I'd been soaking an cleaning the oil pump and it wasn't cutting it (the grime that is). The ultrasonic left everything I tried looking great. I'm going to start doing the rods, lifters, pushrods and other parts in it tomorrow. I can only fit one set in at a time, but it cleans up fast so I should get through all tomorrow.
The photos are of the second camshaft and a comparison of the "new" lifter with the bad one off the original machine. I show the two lobs that are pitted. Bad enough but still better than the other.
The crank looked pretty good in this second engine so I'm thinking about sending it off for eval and possibly a regrind rather than buy another new crank for that engine. | | |
|
| 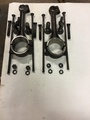 09:12 07/25/17
| 09:11 07/25/17 Cleaning partsYesterday, the ultrasonic got a workout, the job is coming out well though. I found the solvent getting so dirty, that I had to stop and fashion a filter to clean the solvent. That will be today's first job. I'm using a cottage cheese container with coffee filter, set in a cardboard holder to dribble the solvent through after first dumping it out rapidly into another container to get rid of the sediment.
Camshaft is in for weld, grind and heat treating. One more issue out of the way. Since our supplier for refurbished cams (for the Allis-Chalmers) is no longer able to supply us, I'm thinking of putting together an application for the site that would let the community post machine shops they've had success with in their local areas. I was impressed that for about 120 dollars, I should get a like new camshaft.
Oil pump required purchasing a separate kit we carry, it has new vanes, gaskets and springs. What isn't available anywhere, is the relief valve ball. The earlier D series Gnnn engines contain ball valve, approximate 5/8ths in diameter (need to mic it, that was eyeballing to the tape measure) with a spring pressured from the front plate of the engine, pushed into the camshaft front surface (think of it as a tube in line with the oil pump at the rear). I got to looking closely at the ball (basically just like a steely marble) and it's deformed from years of use. It suggests to me that the pressure has been less that it should have been for many years as that relief valve had to be leaking. I found a source but unfortunately, they sell in lots of 10, 100 or 1000. I could foresee rebuilding a few of these, so the 10 will suffice. I also need to decide on the material, carbon steel, stainless, chrome, and tungsten carbide are available. It concerns me to put too hard of a material in there, because one wants the ball to wear, not the face of the camshaft. Not being an engineer, I'm going to go with the softest material unless someone has an opinion... I should take that question to the Tractor Talk forum.
On cleanliness, I've always kept the shop dirty. After my trip to my brother's shop at the airport, I was very impressed by the orderly and clean environment in the rebuild room. Two 8x6 table tops, clean, old parts laid out on the first table, new and cleaned reuse parts on the second table, engine stand in between. Parts and assemblies were laid out in the same order on both tables. I'm trying to emulate that a bit this time. I'm hoping that being a bit fastidious, will contribute to a superior rebuild. After thinking this through, I'm not sure how I even got a ring job to hold together in the past. Age certainly changes one's perspective on the right way to do things.
On reexamination, I found one more slightly bent push rod. I think that is 4 total so far. Thankfully, I have a good supply from years of tearing down the BE/CE engines. | | |
|
| 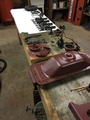 11:05 07/26/17
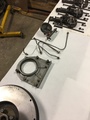 11:05 07/26/17
| 11:05 07/26/17 Oil PumpThe oil relief valve on the front of the cam has a ball that seats against the came. I've purchased 10 SS316 stainless loose ball bearings (because that was the smallest quantity I could get). I went for 5/8s because the micrometer showed between .622 and .623. The .625 of the 5/8s should give me a 2 or 3 thousands to smooth the face of the camshaft's mating surface. I'm going to use a valve seat shaping cutter for the old 60s Honda 50s (remember the Cubs and Super Sports?). My brother has a pile of these from his days as a Honda Motorcycle dealer, they were the factory tools. I just want to touch the face as little as possible, and these seem like the trick for that.
If anyone needs these relief balls, I have extras now and can be contacted through the Yesterday's Tractors. Believe it or not, with shipping they are $10 apiece. Since there is shipping again, it would only make sense if you happen to be making an order, if I know about it, I can toss one in gratis and it wouldn't change the shipping. I'm keeping two so there are eight left. I'd suggest to the sales people that we put it on the catalog, but until I run it in mine and see how the oil pressure works, that would be premature. I'm also thinking about the springs associated with the relief valve. Finding a source for new ones would really help the oil pressure. I think most of the time we are stuck with worn out used springs and that doesn't make sense on a quality rebuild. Increasing the size of the ball should help, but having fresh springs seems more like doing it correctly.
The pump itself, as I removed it, has it's tapered blade edge facing the wrong way according to two manuals. I'm rather shocked because I doubt this has been removed in the life of this tractor. The tapered edge is supposed to be facing the direction of rotation. Some quick figuring says that the crank turns CCW when viewed from the back of the engine, thus the cam should turn clockwise when looking backward, meaning the bevel edge should face toward clockwise. Mine were facing the opposite. Both manuals specify it facing the direction of rotation and the diagrams even show it opposite of how mine came apart. I guess the new vanes will have to go in the opposite way. It would have pumped either way though pumping characteristics would be different (from my study on water pumps, vane direction is only important in changing the volume under different rpm scenarios). EDIT: the vanes were absolute backward all these years. It may have contributed to the demise of those bearings. I removed the oil pump off the other engine and it was opposite. Since only one face of the vanes moved circularly against the case of the pump, the scoring clearly shows which side was out, and the vanes were opposite of what the manuals say.
Cleaned up more parts. Had to filter the solvent as after just a few trays of parts, the ultrasonic wasn't doing as good of a job as I'd like. I'm using cut simple green which is not that great of a solvent, but is a lot easier to dispose of. It was pretty filthy and oily and would clog a coffee filter in about a cup and half of solvent, I started using paper towels stuffed in a cottage cheese container with holes cut in the bottom, and it worked better. Still needed many paper towels before I could get through the entire vat. the scum at the bottom was about a 1/16th inch thick. I also put some painted parts in like the oil filter housing and oil lines. It did a great job of melting off the old paint, it took a quick swipe with the fingernail to leave a bright shiny surface (at least on the oil lines, the filter housing is pot metal and never looks nice bare). I'm running the US temp at 50C. | | Comments | kevinthefixer 05:46 07/27/17 | Chris, a procedure I recommend: use a lathe to drill a hole centered in an extra ball, maybe 1/4", run a bolt or allthread through it, chuck it up in a hand drill, coat it with valve grind compound, touch up the seat face with that. I'm worried about the valve seat cutter not being centered, the tool I just described will self-center. BTW the same shop that can recondition your cams should be able to do the same to the lifters. Does the block have removeable cam bearing shells? | YTSupport 06:17 07/27/17 | That is a great idea. Thanks. On the cam bearings, yes, they will install them if I can get them down to them prior to finishing their job. I have done it myself in the past though with the other AC engines I've done. |
|
|
|  | 21:04 07/27/17 Parts arrivalI got side tracked working on my chipper today for my shop time, but managed to clean a few parts in the process. The big news is the Crankshaft, Cam, main, and rod bearings, liners, pistons, rings, pins, and gasket set all came in. Beautiful parts. I have to clean yet another bench to make sufficient room, but after I do, I'll shoot some photos. The good news is I caught the shop before they finished the block, so they will do the cam bearing installation. The only internal style bearings I'll have to do are the governor bearing and bushing. That's a benefit because visibility and access are great on it, unlike the cam bearings.
I also received my Persian #1 today, so I'll need to find the best thinner for it. I used to use Xylol and still have some. I bought an HVLP a couple of years ago to paint / finish guitars and would like to get the paint to the right viscosity to use it. Perhaps as a blessing, my high-pressure paint gun simply disappeared from the shop a few years back.
My bad news is that it appears I must have given away my C60/B125 stationary engine bell housing. It means I won't be able to fire this up on the shop floor as I'd hoped. I can just imagine someone bought a B, C, or CA from me, and I threw it in. Did the same thing a couple of years ago with my large pallet forks when I sold my AC 816, a really nice kid bought it and I told him "You may as well take these". I kick myself everyday now that my son bought his Oliver 1950FWA. They would be so useful. I vowed to myself to stop giving things away. We are getting a new sawmill soon and we will have to get some. | | Comments | kevinthefixer 20:05 07/28/17 | Can't stand the HVLP guns myself, you can't set them down on a flat surface! But my old-school gun has had it, and no kit available. Better the shop installs the cam bearings, it's so easy to get just one out of line just enough to seize it up unless you have the right tool. I could use a set of bucket forks myself. |
|
|
|  | 20:58 07/29/17 The wrong clutch?(Edit: it may not be the wrong clutch, manufacturer says it will work for all D14s whether they have the old or new flywheel), I'm going to test that out, even if it means pulling the engine back out, have good confidence it will be okay based on measurements, I'll change this section after I get it together) I got the clutch kit and then looked at the parts manual. The D14 (and D10 D12) had two different flywheels in 59. This kit is for the second flywheel using a pilot bearing. The measurements were off by 3mm and I'm not willing to put it in and see if clutch and pressure plate together would work with the older flywheel. Anything involving pulling the engine back off is too difficult with the D14. The difficulty is that the engine is not a fully stressed member as so many of the other machines are, making the front end very heavy when pulling it out. I'm going to pay the restockage and get the right one. If anyone comes across this when getting ready to order their parts, the pilot bearing is a dead giveaway, if you have one, you need the later clutch and pressure plate, if you have a bushing, it's the older flywheel and pressure plate. There is a possibility it would work but I'm not willing to chance it.
Lots of cleaning today while working on other things. I just ran ultrasonic loads while working on the chipper and my son started rebuilding the carb on his pit bike so I helped with that. Actually got quite a bit done, but was unhappy with the mishmesh of pan bolts on the thing. Suggests this engine was opened before, but someone hacked a lot of too long bolts in with extra washers. I'm going to have to find a source for fairly authentic bolts to clean up the mess.
The ball valve balls arrived today and look perfect. I did a leak test on the extra camshaft I have and it was tight. Now if only the cam I'm having reground will be as good. The ball bearings worked out to nearly 10 bucks apiece, but they should be good. Now if I can convince the parts guys to list them (if they work),
I also received a nice set of thread chasers today. I've always used taps and these are supposed to be easier on the threads. I love getting all the parts to go in like a new tractor.
I was looking over the tractor and it wouldn't make sense to not rewire it right now. I need to pull the tank anyway to clean it out, and that leaves everything so open. Of course that means some new gauges too since some don't work. This could easily turn into a full restoration if I don't draw the line some where.
Well, not too much work yet, but I'm mostly pleased. And though it's not part of this rebuild, at least the chipper is running like a champ now, well and my son's pit bike. | | Comments | kevinthefixer 19:48 07/30/17 | Thread chasers are a good thing, rather than cutting off the metal like a tap does, they bend it back into shape. Beware of grit in the holes though, and lube them up. WD40 works with them, and it's cheap enough to use as cleaner too. Want your threaded holes to stay like new? Use a q-tip to smear a bit of anti-seize compound in each before assembly. Not a gob, that might crack the block if there's not enough room for the gob and the bolt both in the hole. Just a smear, enough to see it and no more. |
|
|
| 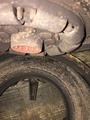 10:38 07/30/17
 10:38 07/30/17
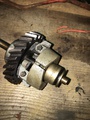 10:38 07/30/17
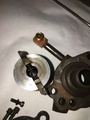 10:38 07/30/17
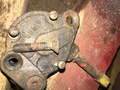 10:38 07/30/17
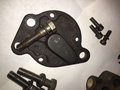 10:38 07/30/17
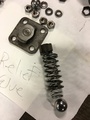 10:58 07/30/17
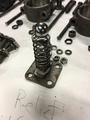 10:58 07/30/17
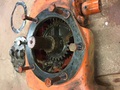 19:16 09/08/17
| 10:38 07/30/17 Which direction/oddities?Some notes which I will add to as more things arise. Might help people who disassemble things without noting the orientation of parts. These notes apply to D14 and numerous other G149 applications.
1. Clutch direction. The clutch plate has a long and short side on the 1 1/8 inch spline that fits over the main shaft. The long side should point toward the rear or tractor seat. For the early engines with the spring clutch disk, this means the springs on the clutch plate are facing the rear too. This applies to engine numbers G149 11075 and older. The others may be similar, but I haven't tested that yet. The later version clutch also has a (less pronounced) long and short side.
2. Governor Thrust bearing. The governor has a bearing at the end of it's shaft that can fit on the shaft either way. It should have the thrust washer side facing the front of the tractor.
3. Oil Pump. Vanes have a beveled side. That side should point toward clockwise rotation.
4. Oil Relief Valve (front of camshaft). The thrust plunger has a long and short protrusion, the long side faces to the rear of tractor and the spring goes over it. The second inner spring just rides on the surface as plunger is to remain spinning with camshaft, ball, front plate and thrust surface remain stationary to engine front cover.
5. Oddity about oil pump covers. Some are countersunk using appropriate beveled bolts, others are flush mount and use standard bolts. Just a note for anyone getting a pump from a junk yard, get the bolts with the pump. The two photos are from tractors built near the same time. The BE/CE engines use standard bolts yet the same cover as the D-series. It's odd that this countersunk version would appear.
6. D14 Steering housing assembly bolt pattern. The 1 1/2 inch bolts go front and back center, the 2 1/4 bolts go both sides in the front, the 2 3/4 bolts go on both sides rear. Front as sitting on the tractor seat. Why the odd sizes is not intuitive. | | Comments | kevinthefixer 19:55 07/30/17 | I used to think you shouldn't be working on stuff if you couldn't remember how to put it back together. Well, they say the memory is the second thing to go, forgot the first one. The good news is that top-quality photography is now available to nearly everyone, certainly anyone who can afford to rebuild a tractor, and you don't even have to have pics developed. I can't imagine taking apart an unfamiliar machine without a camera handy anymore! But when my 'phone has an excellent one, there's always one handy. | YTSupport 07:19 07/31/17 | The problem gets worse when you have years between teardown and assembly. As I've been doing this, I keep an eye out for anything that could be confusing to someone and then snap a shot of it. As far as memory and age goes, I pulled 6 cap screws out of the ultrasonic and could not remember what they were from, just an hour from the time I put them in there. Admittedly, they were some I tossed in with the another batch of parts I was working with and turned out to be from the pressure plate which I was not even thinking about. But memory is frustrating. |
|
|
| 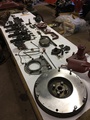 07:53 07/31/17
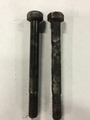 07:53 07/31/17
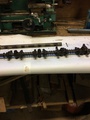 07:53 07/31/17
| 07:53 07/31/17 Full TableThe cleaned parts bench is getting full, I have only the governor case, carb, and a couple of clean and paint tasks on sheet metal before it's time to sit back and wait for the machine work to be done.
I pulled out the head bolts and started to clean them. I noticed two of them had been in a bath of coolant for some years, possibly due to the leak. They looked like a snapped bolt waiting to happen. I luckily had a couple of brand new bolts to replace them. That was fortunate since head bolts have a nice machined surface to mate well with the head. The damage to the bolt from rust looks very long term. It does beg the question, did I really know where the leak was, why would these bolts have been submerged in coolant? I thought it was an o-ring on the sleeve, but I'd better look very closely for cracks when I get the head and block back. The coolant should not have been able to work past the threads and bathe the bolt shank. A mystery to solve before assembly.
Short header studs were shot, long ones were good, but one is missing somewhere in the shop. The long one may be difficult to replace. I found the right length for the short ones at a speed shop in California so I'm having them ship me four of them, and replacement lock nuts for all 8 studs.
Disassembled the rockers and put them on a clean pipe so I could keep track of exactly what was where while cleaning them up. It's a foregone conclusion replacement of anything on that shaft will be difficult at best. I'll be cleaning and lubricating but that's about it. | | Comments | kevinthefixer 19:00 08/01/17 | Before you get the head and block back from the machine shop, ask them to magnaflux both. That will show any cracks beyond any doubt. If your bolt holes go through to the water jacket, yes, coolant will follow the threads right around and soak the whole bolt, and probably leak around the bolt head a bit. Coat the threads, both bolt and hole, with brush-on Permatex #3H non-hardening sealer. There are knock-offs, I recommend stay with the original, I've been using it at least 45 years and seen nothing I like better. Take a good look at the surfaces where the rockers hit the valve stems, correct any pitting there. This one I'd tackle myself, just find some hardened steel rod and melt it into the pits like it was welding rod, with an acetylene torch, grind back to shape and polish. | YTSupport 10:26 08/02/17 | Yep, they will do that, check for cracks. I have read that if sealer was not used, it could have caused this, it appears that bolt was submerged for a long time. I managed to find a complete set of lifters with no pits. For the next engine, I will have address them. | kevinthefixer 18:40 08/02/17 | Guess I didn't make myself clear, I meant the rockers, not the lifters, they can develop pits where they hit the valve stems. For some reason they don't ever seem to have problems where the pushrods contact, maybe because the valve stems don't (hopefully!) move back-and-forth in relation to the rocker shaft. But if the case-hardening cracks off the rocker it's a matter of time before both rocker and valve stop doing their job. I don't need to tell you that now's the time to fix it if there's any damage. |
|
|
| 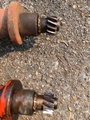 07:03 08/03/17
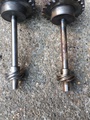 07:03 08/03/17
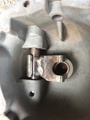 07:03 08/03/17
| 07:03 08/03/17 Governor/DistributorI was pulling the distributor from the housing it mounts on since that housing required replacement (broken flange). I looked closely for the first time at the drive gear. The wear on it makes me wonder how this tractor ran at all. Compare the top gear to the bottom, the bottom is what came off this tractor, there are nothing but sharp curved teeth left, un-servicable. The same was true with the governor gear that drives it. I hadn't looked closely at the gear even though it was already cleaned. The governor on the left is the one from this tractor, again an unusable gear. Fortunately, we have both parts available off the shelf.
A part we don't have available, is the governor housing. AC built this such that the throttle control shaft is integral to the governor handle. The shaft and bushings were installed, then the tab that contacts the thrust bearing was welded on. It makes it impossible to refresh the bushings. There is enough slop in the bushings that it is going to leak. I now see why someone had jury-rigged the two control arms with a wire to hold them down. Keeping the shafts from rising would have kept the leaking down. It can be replaced once on the tractor if necessary.
I disassemble the carb and once again was surprised at how bad it was. We have a basic carb kit that covers all the Marvel-Sheblers, so I will clean it in the ultrasonic and try that first.
I had to remove the tach gear to clean and transfer to the new housing. That's when I realized that the end of the cable had come off long ago. That explains why the tach never worked, but it does mean the gauge itself may actually be functional. I'll start exploring options on how to deal with the cable. Seems unlikely that a 60 year old cable from a boneyard would be worth bothering with.
Each disassembly and inspection makes you wonder how this old machine ran, and it ran quite well.
Edit: CE/BE engine governor covers are exact duplicates for the D14 and other G149 engines, so most governor covers from an AC IB, B, C, CA, B125, or C60 will bolt right up, even from the magneto style. I just happened to have a good one. My recollection was that they had a slightly different arm, but the remaining ones I have here are identical. The oil fitting must be swapped since the oil fitting has two outlets to cover the distributor oiler. Most BE/CEs had magnetos and didn't have the second oil line coming from the governor cover. That is a stock part from any hardware store though. A female to dual male NPT brass fitting. | | Comments | kevinthefixer 19:25 08/03/17 | Suggest you get a new float for the carb also. When I did mine, I gave the float a pass; it was light, had no visible damage, no liquid in either chamber, wasn't even out of adjustment. Two weeks later it started flooding, found both chambers half full of gas. Must have cleaned some varnish out of the one 'cos it was leaking in a spot where nothing could touch it. The other had dropped down and scraped on the far side of the bowl--I'd failed to set the drop (I still don't have a spec for drop but I faked it). Seems I must have used a needle seat with a slightly smaller OD, allowing the float to drop too far (drop is controlled by the little flat tab that sticks up from the crosspiece at about 90 degrees, it hits the outside of the seat tube). So please learn from my screwup! | YTSupport 07:04 08/04/17 | Point well taken, I was thinking I'd tie the float to the bottom of the ultrasonic cage and put it in under 40C heat for 30 minutes under 4 inches of solvent. If it's sunk when done or won't clean up, then the new ones are cheap and we have them at the warehouse. Carbs have been a continuous battle this summer with all the small engines I have here. The ultrasonic seems to do a good job without damage (though I bought it for reloading, it's been used almost exclusively for tractor parts and carbs). |
|
|
| 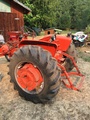 12:50 08/06/17
| 12:50 08/06/17 Unserviceable MemoryI completely forgot the most important step in rebuilding that I learned the hard way. 20 years ago, I rebuilt one of my CE engines and didn't recondition the piston rods. I bent one in that engine and ruined the rebuild, I'd suspected it had a twist. I even keep that rod around to remind myself. I was cleaning the shop to get ready for taking the tractor outside, cleaning and setting it back up in the space where the reinstallation will occur. During cleaning, I ran across my pretzeled rod still attached to a brand new piston and it clicked why it's there. I'd like to think I forgot because the rods look so good, but the fact is, it must be age, because now I remember how hard over I was on the importance of reconditioning your rods. So the rods go in tomorrow for reconditioning. 25 dollars a cylinder well spent.
The clean up is done on the tractor and I'm tracing the wiring to make my working schematic for the rewire. Wiring is identical to the original manual thus far other than a circuit breaker I put to replace the shot fuse block, and the ballast resistor put in when it was converted from 6V.
From the photo, you can see the Persian #2 from 25 years ago held up quite nicely, though of course is the wrong color. We only carried Persian #2 when this tractor was painted. It was worked hard and the paint did it's job, plus it doesn't appear to have faded as people so often say. I picked up very little rust over the years. Paint was Tisco. New will be too, only the right color.
I cleaned the tank with a mix of cider and white vinegar. The little rust it had, disappeared, though I am worried about picking up rust prior to filling it (which could still be a month). I'm going to flush it with backing soda, then try denatured alcohol to rinse the moisture out, then leave it in the dry 80 degree sun today. I'd never used vinegar, but the price and deposable nature of it really appealed to me. I did a test first with just the cap, which was by far the worst rusted part of the fuel system. I didn't brush off the scale or touch the rust, just set the cap in a bucket of vinegar. After about two hours, I saw gray metal spots forming. After 5 hours, the cap had no signs of rust. Now if only someone would tell me a homespun safe substance for paint removal.
Since we sell Red-Kote, I was toying with the idea of that, have had good success with it, but this tank just seems too clean to start a cycle of tank coating. | | Comments | kevinthefixer 19:33 08/07/17 | Can you leave your tank sitting in an air-conditioned office? AC acts as a dehumidifier. You could also coat it with motor oil inside, when you do fill it a little extra upper cylinder lube during break-in won't hurt a thing. | YTSupport 08:30 08/09/17 | Something like that works. I was going to spray it with LPS and then flush that with alcohol before filling it later. It is unfortunately going to sit for a long time since I just sent the rods in. Of course the block and head aren't back yet either, and now that I've started the teardown for painting, that's going to be a month just by itself. |
|
|
| 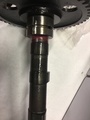 11:49 08/11/17
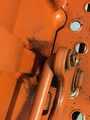 11:49 08/11/17
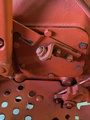 11:49 08/11/17
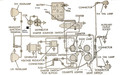 09:32 08/12/17
| 11:49 08/11/17 PTO leak and liftersI got the camshaft back and it's beautiful. My brother and I were looking over my collection of readied parts and he convinced me that since the only thing I haven't refurbed are the lifters, now is the time to do it. It would be a half-way job if I don't do that. So the lifters will be sent off this morning to Delta Camshaft in Tacoma for a reconditioning. I keep trying to be cheap, even now.
The PTO o-ring is leaking and since I'm now painting the entire machine (interesting how these projects grow, but I have the time, it will be a long time before the rods and lifters reappear, and I still don't have the block or head). The first shot is the PTO lever which is right above the clutch shaft. It bathes the clutch shaft in oil, not a drip, but puts a sheen on it and then dust turns it to sludge. It requires a split at the transmission which now, since the engine is still out, it's an ideal time to do that, but just the removal of the Traction Booster and various other components, makes it a big job, plus I have only one hoist. I'm going to pull the right and bottom side covers and see if I can't figure a way to pop the roll pin out and remove the shaft while the Power Director remains installed (unsplit). If that doesn't work out, I'll have much of what's needed to split the tractor at the transmission case already done. If I can get the roll pin out, I will replace it with a shoulder bolt and Ny-lock since this shaft appears to have virtually no stress on it. It's not a shear point and it's use may have been a cost saving factor. Can't see an engineering reason in this application.
I included the ops manual wiring diagram. I checked mine over and made the changes that were made to mine with the exception of there being a circuit breaker on the light circuit rather than the fuse. I should locate and restore it to a fuse since the side cover has a hole where you are supposed to have the fuse block protrude. Ignore the 3 cell 6 volt battery, it's a 12 volt. | | Comments | kevinthefixer 12:18 08/12/17 | You're running an external ballast resistor without a bypass circuit? Adding one will help with starting if the battery gets a little low. If you're lucky the 12V solenoid will have an extra terminal (usually marked I for ignition), just run a wire from that to the coil side of the resistor. If not run from the start terminal (keyswitch or solenoid) through a diode to the coil hot. Might save a lot of cussing on cold mornings. |
|
|
| 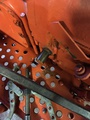 21:30 08/12/17
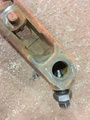 21:30 08/12/17
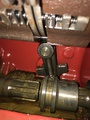 21:37 08/14/17
| 21:30 08/12/17 Removing Power Director ArmI'm not sure why, but never having removed that arm, I assumed it was likely a splined shaft. Got to looking at it and it was a lot simpler than I realized. I thought I'd put some photos of what it and the detente lock look like. Nothing magic, It just took a 2-jaw puller to get it off, it was not going to pry out off there for anything. The photo shows it after some clean up with steel wool, but it was very rusty having never been off. You'll notice it has the set bolt so there is only one way it can go on, you don't need to mark it's position on the shaft. It locks it to position and adjustment is made by adding and removing washers to the forward position.
The detente is that stub of steel sticking out in the upper left of the picture.
The cover behind it is what I'm going to remove to attempt to access the PTO shifter to replace the o-ring. I'm really hoping it will have enough clearance to get a puller in there to remove the roll pin. It will save me a couple of days (of course it might incur a couple of days making the pusher to push the pin out ;)). I'm assuming the pusher will be something like they make for the AR-15 trigger. If this works, I'll do a separate blog on it.
Edit: I just added a photo of the PTO arm from the inside. You'll the the upside down T casting and the shaft coming through with the roll pin hole peeking out from the right of the photo. I stared at this for about 4 hours total now and can imagine the puller I need to make. Anything I do involves welding or machining so I either have to go to my brothers or fill up my wire feed argon tank (which hasn't been used in 15 years, will they fill it... one wonders). I tried tapping it out today with a perfect sized allen socket, but that had no effect on it. It's not interested in coming out without a lot more force than I can get putting my hand through the small case hole and not getting much force from a piece of iron swung by wrist motion. I think I will have to head to my brothers shop and machine something that will push it out. It will be a handy tool for shafts if it can do more than one job.
I also took the old and new cranks to a shop today. I had enough on my hands and told them to swap the timing gear from the old to new when they had time. I have too much on my hands here and don't own a press. I didn't want to break that gear.
I spent some time in our warehouse and pulled some Ford NAA reproduction hose clamps out of inventory and matching them up to the originals still present on the D14. They are a direct match. I also discovered our Farmall fuse holder is the same that originally was on the Allis' also. I don't look forward to rewiring and replacing most of the gauges, but it doesn't make sense not to as far apart as I have this thing. I'm still waiting on the block, lifters, head etc to come back from the machine shop, so I have the time. The PTO shifter may take up all that time though, I probably should have split the tractor. | | |
|
|  | 10:58 08/16/17 MiscellaneousI got back the crank with the gear pressed on. Shop time $40. Given the price of a press, I should have bought a press, I'd break even very quickly, but that is one more item down.
The removal of the PTO shifter may have taken a step forward. I bought a hinge removal tool for antique autos. I got it from Mac's because they were the only company who would respond with dimensions. It's a small press with 2 7/8s space between the jaws and a total of 5 inches long. It should fit in the Power Director case with room to spare, which it will need because I'll have to turn a 9/16s wrench inside there to operate it. We'll see if it works when I get it. I will pick up a dowel to reinsert into the shaft hole while we have the PTO shifter out, just to keep everything in alignment. I will have to check the diameter and add that here.
I decided to use an 8N Conversion alternator as we keep them in stock at the warehouse. With it, I can use our standard AC mounting brackets which we also stock. I hate to see an alternator on an antique tractor, but the way the D14 is designed, removing the starter is a hassle due to the regulator positioning. By using this self-regulating alternator, I can toss the regulator and simplify the wiring dramatically. I don't show tractors, I use tractors, so it's a pragmatic decision. Tossing the regulator will leave a massive space in the compartment between the side sheets, future work on the tractor will be enjoyable rather than the pain it's always been. Now I'll need to modify the wiring plan.
I'll be using the original pulley and fan on the alternator just to keep alignment perfect. It's about a half size larger meaning the output will be lower on the alternator. I am banking on the possibility that the output of the alternator is such overkill, that I can get by with it. The rest of the measurements all check out so I'll swap them today.
I cleaned up the dash light yesterday, it looks like new, just need to get some low gloss black for it. We stock a replacement that looks identical, but it's chrome like the later D-series and I wanted this one to have the black like all pre-mid-59s. Other interesting black parts that I wasn't aware of was that the fan should be semi-gloss black as should the starter (and generator if I were using it). All the lights will be too, I just ordered replacements for the fronts and bullet tail lights. I've had non-standard work lights all around for years. I'll put a single rear work light from the aux outlet on the seat mount, which was an option you could get originally though it required drilling the wheel guards (fenders). There was also an optional horn according to the parts manual, would love to do that, but I have no idea where it mounted nor where the dealer would drill the hole for the horn button. | | Comments | kevinthefixer 19:49 08/16/17 | Maybe the horn mounted with a clamp on a lever somewhere, and had a rubber bulb to squeeze? Seriously, you know what a tractor sounds like, what earthly use would a horn be? | YTSupport 07:46 08/22/17 | I have one of those of an Indian Taxi, basically a Bugle with the mouth piece soldered over. I know they are useless on a tractor, but it always fascinates me to find something in the parts book that I never saw out in the wild. |
|
|
| 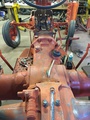 08:09 08/22/17
| 08:09 08/22/17 Just waiting nowI have everything but the tool for fixing the PTO lever o-ring, block, head and rods. While I'm waiting for all those, we've started to clean up the main frame in preparation for painting and wiring. In this photo, you can see how much space there is now behind the instrument cluster. Without the Voltage Regulator, it has room for all manner of wiring. We're going to paint the space first since with the side panels on, it will not be painted. AC left the interior primed, but we'll hit it with Persian #1 prior to wiring up the new gauges and closing it up.
I've spent a considerable time studying Ammeters and looking at alternatives for hooking it up. It seems a shame to put a non-branded voltmeter in the cluster and leave the 60 amp AC branded ammeter out, but then the primary has to run all the way to the ammeter and that introduces more chance for catastrophic shorts later on. Still thinking and studying schematics of how people have retained originality yet upgraded for safety. | | Comments | kevinthefixer 19:25 08/22/17 | Just a thought: is the shunt on the stock ammeter external? If so, you could mount it on a terminal block close to the starter solenoid and run very fine wires up to the gauge itself. Otherwise, you could put 100A fuses on both wires going to the ammeter, and/or double and even triple insulate them. Perhaps run 10 gauge insulated wire through 1/4" fuel line with that stainless steel woven cover you can buy at hotrod shops? Keep that away from the exhaust and the fan and it would take a chainsaw to cause a short. | YTSupport 14:46 08/25/17 | Great ideas, but I'm starting to think I will bag the idea of using the alternator and just buy the smaller voltage regulator that is made to fit in there. If I reuse the Generator, it's impossible to produce enough amperage to blow out a 60 amp ammeter. I also just had some pangs of getting back on the originality kick. | kevinthefixer 19:44 08/26/17 | So far I've been able to use pretty much all my original hard parts, mostly 'cuz it's been cheaper to fix them than upgrade. Specifically the charging system, which reminds me that I need to ask John Saeli if he can perform the same miracle on the generator bushings as he did on the distributor bushings. I once made a starter bushing for my '75 Norton, but I no longer have access to a lathe. | YTSupport 07:12 08/27/17 | I have a small lathe and it does come in handy. So far though, every bushing I've needed has been available. One of our salesmen has been cross-referencing and even though we don't list all the seals and bushings, he's been able to set me up and I guess does that normally if people call in an order. Shame the catalog takes so much update to reflect all that stuff. I've been leaning back toward using my generator and just paying the 16 something for the smaller correct voltage regulator. The wiring is way easier because the generator can't produce the amperage to destroy gauges and such. It'll be more original that way anyway. |
|
|
| 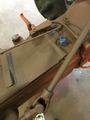 08:36 09/05/17
 08:36 09/05/17
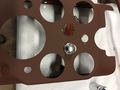 08:36 09/05/17
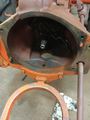 08:36 09/05/17
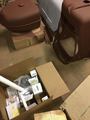 08:36 09/05/17
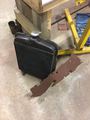 08:36 09/05/17
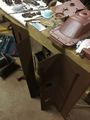 08:36 09/05/17
| 21:33 08/29/17 Slugging through the prepSince I've been waiting for the parts to come back from the machine shop, I've spent most of my time cleaning, sanding, and wire brushing. I have pulled the covers on the PTO and Belt Pulley case, just to make sure they are tight and won't mist oil out. The PTO uses an o-ring on the seal retainer so though we had the seal in stock, the o-ring is a generic item, and I've ordered the 2 7/8s required. I checked the transmission case cover and hopefully it's tight enough to go for a few years. I didn't want to remove the shift forks when all is functional there. I am concerned about the front seal and probably making a mistake by not replacing it. The front of the torque tube was packed with thick grime.
All the removed parts have been primed and I have my doubts about the the little turbo HVLP unit I'm using. It worked great for primer, but it doesn't feel right, not enough adjustability to crank down the paint flow. I'm probably going to have to replace my compressor before I start the color and clear coats. It's not producing enough air now to even catch up to cleaning chores. Unfortunately, that, replacing the shop lights (to accommodate the onset of fall), getting my new sawmill set up, and painting all the outbuildings, is going to slow down the tractor restoration. But, I have a new toy coming that will fulfill my tractor cravings for the moment. A D12 will be here within a couple of weeks. That will be the next restoration I'm sure (or the IB), but it already runs and will be great to play with for awhile.
In the photos, of particular note is the dash showing the fit of the new lighter, reasonable replica of the original. Also, I'm happy with the results of the torque tube cleaning, gone is about an 1/8th to 1/4 inch of grime. One thing that concerns me, is that it could have been that seal where the main shaft comes out. If I don't replace it now and it is bad, that would be a terrible amount of extra work later. I assumed the rear main was leaking causing that grime. | | Comments | kevinthefixer 18:45 08/30/17 | Looking forward to that! | YTSupport 16:28 09/04/17 | Sorry about, I completely forgot, it took me forever, 3 solid days at the computer to figure out what wire I wanted and find a place that had quality wire by the foot. I was going to Mil Spec aircraft wire, but couldn't find the colors. I finally finished that up just a couple of hours ago and got it ordered. I'll get some photos tonight, almost everything but the main frame is primered. |
|
|
|  | 17:00 09/04/17 Wiring purchases/notesBelow is the result of the painful process of finding quality wire, in the right colors, in the small amounts needed for a tractor. I finished that today and the wiring bill is a shocking $100.00. I also finally found and purchased a lighter that is as close to a replica as they get based on original AC video and the ops manual photos. I found it at OReilly of all places. Part No 10212. I also discovered that our (YTs) DR replacement voltage regular has a poor description. It's the four lug version I need but looks like only 3 in our catalog. The G terminal is underneath it. Need to correct the part description.
Kevinthefixer suggested I shunt around the ballast resistor for a hotter spark starting. I may add in a line from the momentary side of the starter button to the - side of the ballast resistor to accomplish that. Since the battery will be heavily taxed and voltage dropped, it should keep the points from frying.
Note that I am using way too much #10, the thing could have been wired with #12 throughout given the short distances and low amperage. I just chose where I wanted to put the fuses and stepped down to 12 at that point. Here's my wiring notes that led to my purchases:
1. (2) Blue 10 wire 5 feet minus ammeter to mains on solenoid (plus battery connection) 2. (3) White 10 wire 5 feet starter switch (engaged) to solenoid trigger connection 3. (5) Red 10 wire 5 feet B terminal on VR to plus ammeter 4. (6) Green 12 5 feet F terminal VR to F terminal generator 5. (7) Brown 10 5 feet G terminal VR to A terminal generator 6. (8) Black 12 5 feet L terminal VR to starter switch input 7. (11) Green 12 3 feet starter switch input to fuse block 8. (9) Yellow 12 1 foot starter switch input to ignition input 9. (10) Yellow 12 7 feet ignition switch closed to ballast resistor 10. (10) Yellow 12 1 foot ballast resistor to plus coil 11. (17) Yellow 12 1 foot coil minus to distributor 12. (12) Purple 12 3 feet fuse block to light switch input 13. (13-16) Orange 12 15 feet light switch closed to dash, tail, aux, and head lights 14. (4) White 10 1 foot plus ammeter to cigarette lighter
(numbers in parens correspond to original Allis Chalmers D14 wiring diagram, I and T copied the chart but recolored several key wires, using AC docs.)
Buy List: Blue 5 feet 10 White 6 feet 10 Red 5 feet 10 Green 8 feet 12 Brown 5 feet 10 Black 5 feet 12 Yellow 8 feet 12 Purple 3 feet 12 Orange 20 feet 12
Should be 20amp circuit breaker connected to starter input going to yellow and green wires connecting ignition input also fuse input. This means a short 10 running from starter switch input to circuit breaker. Then lighting system will have 15amp fuse. Update, the 20 amp circuit breaker also needs to pick up drawing 3 white wire to solenoid. Or we could put it at the L terminal of the VR, allowing us to use black 12 gauge to starter button. 30amp fuse at B terminal of VR just for fun.
Should use SXL rated wire, high abrasion protection in casing. Update: settled for TXL because of purchase problems. I need so little wire and you can't by SXL or Mil Spec in anything but rolls that would wire 20 tractors. | | Comments | kevinthefixer 19:19 09/05/17 | DO NOT SIMPLY WIRE A SHUNT FROM IGNITION SWITCH TO COIL! Can cause feedback to the solenoid, holding it in the start position. Either put a diode in the circuit or use a solenoid with an "I" terminal designed for that. Or do without that circuit and make sure your battery is always charged and never frozen. | YTSupport 16:27 09/06/17 | Good to know. I had a couple of shadetree diagrams and was running off of that. | kevinthefixer 19:10 09/06/17 | Yeah, there's a reason automotive solenoids had that circuit built-in. You could also add a Ford-style automotive solenoid into your circuit, run the output of the Ford solenoid to the start terminal of your stock solenoid, and the "I" terminal up to the cold side of the ballast resistor. Any way you can prevent voltage from feeding back to the starter solenoid exciter after you let go of the start button or keyswitch (forget which your wiring diagram showed). | YTSupport 21:24 09/13/17 | My brother suggested a relay which would be kind of cool, but I bought a diode today to put in it. I can't do any wiring until I at least get the dash painted and that will be awhile. I'm still not sure I need the starting spark boost, This tractor always fired up instantly. But it will be cool to have an upgrade that doesn't change the originality (that you can see anyway). | YTSupport 21:24 09/13/17 | My brother suggested a relay which would be kind of cool, but I bought a diode today to put in it. I can't do any wiring until I at least get the dash painted and that will be awhile. I'm still not sure I need the starting spark boost, This tractor always fired up instantly. But it will be cool to have an upgrade that doesn't change the originality (that you can see anyway). | kevinthefixer 18:45 09/14/17 | Your bro's a smart cookie. That is, he agrees with me! BTW a Ford start solenoid is nothing more or less than a high-amp relay. Since you are bending over backwards to keep originality, I suggest you add your diode inside a completely seperate wire harness that can simply be removed. Assuming your connections are ring terminals, just piggyback the extra wire onto the start terminal on your solenoid, solder the diode in the middle somewhere, and piggyback the other end onto the hot side of the ignition coil. Want it back original again, remove it, no harm no foul. I'd put shrink tubing over the diode and solder joints but be sure to mark your polarity, maybe use two different wire colors? And take a pic before covering it all up with the shrink tube? | YTSupport 22:49 09/15/17 | I bought a woven wiring loom from a antique auto supplier and purchased one size larger than I needed. That should let me slip the diode in the loom and no one will be the wiser. I'll use the same color wire as for the normal ignition circuit if I have enough. I didn't plan the circuit when I was doing the purchase. The one thing that will be a problem, is that I purchased two modern style fuses beyond the lighting fuse that will show, Those will be behind the side panels so that's probably okay from an originality standpoint, beyond the fact that if were to blow a fuse, it is a hassle to get into the side panels. I may come up with something where they will be hidden under the hood, but not noticeable. The traditional/original fuse will protrude through the side panels as done in the 58 when it was delivered. |
|
|
| 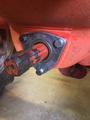 07:18 09/14/17
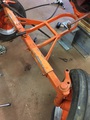 07:18 09/14/17
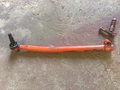 07:18 09/14/17
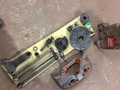 07:18 09/14/17
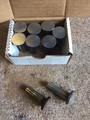 07:18 09/14/17
| 07:18 09/14/17 Front end and liftersI've continued slugging through the process of cleaning and refurbing as I go. I did the PTO seal, and am working on the steering gear. I'll do separate journals on both. The steering gear has taken several days, both in research and work. Hopefully YT will soon be carrying a kit that has everything necessary to refresh the front end and steering. The original seals were very strange with felt and nitrile (probably neoprene in those days) sections, I'm replacing them with modern nitrile. I discovered the seal issue because I decided to fill the gear as specified. The next morning, much of the oil was on the floor of the shop. Neither seal was doing anything. I know for a fact the case had no oil for the last 20 years, and I'd wager 30 or 40 is more likely. Only by virtue of these shafts seldom doing more than 5 RPM were the bearings still usable. They are loose though and I'm removing all shims to take up the slack, I may use Permatex #2 Gasket Maker alone to get a minimum shim effect. Should hold 90 weight fine, first I'll try construction paper and see if the play looks okay. I'll show the highlights in the photos.
I also got my lifters back from the shop. They are beautiful. I have a non-machined one sitting in the photo for comparison. I used Delta Camshafts in Seattle. Good machine shop.
This has turned into a complete restore save the hydraulic pump and transmission. Large job but with the expense going into the engine, I think it's worth it.
I had to buy a new air compressor to do the color and clear, my old one was not salvageable, but it was single stage anyway, and painting with it was always painful. I've been using my little pancake carpentry compressor to blow parts out in the meantime. | | |
|
|  | 09:15 09/17/17 RimsI never thought I'd get so fervent that I'd replace functional rims, but I've gone so deep into this thing, that it's come to that point. One of the front rims was involved in some issue and split then rewelded with a plate in the middle, then redrilled for the lugs. It was a surprisingly good job because the wheel has no wobble, Whatever happened cracked the spindle off which was then re-welded too. On the other side, the rust at the lug mounting points is more than deep, if I get it all cleaned out, I will be seeing daylight where I'm not supposed to. Since I've put so much work into the steering gear, tie rods and such, I should bite the bullet and replace the rims, one of the tires and even the spindle. The spindle doesn't have the camber it should, the fellow welded it perfectly straight.
This tractor is going to be surprisingly new when I'm done, my Kubota will be jealous. But the interesting thing is, that for all the money I'm putting into it, the total price is still a drop in the bucket compared to my modern tractor (an L4800). You could argue that my 4x4 Kubota is a far better tractor, but better is relative. The D14 gets better traction, is far more stable on cross hills (which it better be with no ROPS), and has a couple more horsepower (after the engine rebuild is done). Aside from that, even though the D14 does better hitch work on all but tilling (too fast), the Kubota has a backhoe and loader on it, and they prefer to stay on it, making it a major time waster when I want to do other work. I need both to maintain the farm, and the D14 does it's part of the job a lot cheaper, even with the money I'm spending. If I figure I amortized the D14 years ago and discount it's original price (valid I think), the cost of the restoration is still below the price I could sell it for. I'm justifying, but I think they are rational justifications. Labor of course, doesn't count, it's my version of bliss. | | Comments | kevinthefixer 18:21 09/17/17 | Y'know, as pretty as this machine is going to be, I'd be afraid to actually use it aside from sunny-day parades and such. And although I don't think I'd call it bliss, exactly, I also do this stuff for the warm fuzzy, and I think we're in about the same boat financially too: If we sold our finished projects we'd about break even. For myself, this is the only way I'd ever afford a tractor at all, buy a junker and add a few parts and a lot of sweat equity. Any idea when you'll quit finding more things to fix and start reassembling the ones you've already torn down? | YTSupport 08:42 09/20/17 | The way I figure it, this machine will be "New" for my lifetime even with using it. I try to go easy on a tractor. Backhoe or dozer it's different and they get pretty beat up. As long as I can keep everything shedded, it should stay in good shape. Yes, labor doesn't count, only thing that factor in sale price is condition, popularity and rarity, though I see proudly priced tractors sometimes. I decided the other D14 is parts so it won't be going back together, aside from that, I have a IB, and now a D12 to restore. I'm thinking about D15 Diesel too. I'm going to try and get them all done asap. Life is only so long. This is a cheap and useful hobby, one antique car would be worth more than 10 tractors, and so much of it isn't money, just work. It's still possible to find free tractors as a start. | YTSupport 13:16 09/21/17 | I didn't answer your question about finishing something. The condition of my stuff, is that to do one thing, I need another, that means fixing it and in doing so, needing yet another piece of equipment has to be refurbed. And since I have many unrelated projects with this farm, there is no end in sight. Just doing this tractor, meant getting the pressure washer working, the compressor, redoing wiring and light fixtures in the shop, several small things like going through and cleaning up taps and dies, pullers etc. I may work for two days on this project without touching anything to do with the tractor itself. Multiply this by my other projects around the farm. I will finish, but in the process, a lot of other things will be finished. | kevinthefixer 19:21 09/22/17 | Unfortunately, we are the last ones (at least in this country) to know how much work a farm actually is. Everyone I know, their grandparents were farmers. Most people I know, their parents were farmers, at least as children. Nobody I know is a farmer now unless you count aquaintances here on these forums. Even my favorite cartoonist, Garry Trudeau (Doonesbury; I hope I spelled his names right) thinks farmers have it easy. Well, sorry, you can't eat, live in, or drive anything that ever came out of an office building. |
|
|
|  | 09:04 09/20/17 Shop workMy air compressor went completely south and I can't even paint without it. Since the tank is almost ready to fall over from rust, I bought the cheapest two-stage I could find, I'm having to get it installed and that means no tractor work for a couple of days. I want to put it outside rather than have it in the shop, so there is a lot of messing around to pour a pad, run the wiring and hose, get it earthquake proof. But, I should be able to do better paint work with the two-stage so it's a worthwhile sidestep (plus there was no choice). Another sidestep is getting my welding gear in order, including my wirefeed. A rat made a nest in my helmet over the years, and I think the circuitry is now questionable, so I may need one of those too. This tractor has a few sheet metal spots that need clean up, and I'm thinking of welding up mounts to put a grill in it. So it's time to get back into welding. Been a lot of years. Not a complaint, I like getting the shop equipment back to shape, too many years pounding on the keyboard and letting the shop go.
I did reassemble the steering and dash console just so I can get going on the wiring. There is a bit of clean up left, but I'm thinking I should start the reassembly part of this project (a new project journal). I also told the son to start tearing off everything from the other D14 so we get as much of it out of the elements for the winter. I'm going to use the rims off it for this machine, and try to shed everything that isn't cast into the mainframe. I've already scavenged a few parts from it for this machine, and it's time to admit that it's probably going to be parts, not a another restoration. That opens up the possibilities for using other pieces from it that are in better shape than this machine. I think it's a shame to ever let a machine go to parts.
When I was doing the dash, I had to put the traction booster control arm back on, it can't be mounted after the assembly is on. A note for anyone searching for parts, the roll pin that holds the linkage to the hydraulic pump is 1 x 1/4. Make sure the cup that goes over the pump shaft is clean and lets you slide the cap over it easily. If you don't, you can push the shaft much of the way down into the pump casing with too much pressure and that can't be good for it. It wants finesse. I would really suggest a 1/4 inch roll pin starter as the access is cluttered. Also don't forget to get the traction booster control lever under the left quadrant section. If you don't, you have to take it apart again. It's easy to forget and the spring pops it up above the quadrant. | | |
|
| 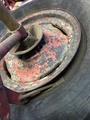 07:31 09/23/17
| 07:31 09/23/17 More Parts RecoveryI unfortunately wasted several hours trying to save a part that was beyond hope. I needed one good 4.25x16 rim since one of mine had been split and a plate welded on for the lugs to bolt to. I wanted to replace this one because it's pretty bad looking even though functional. I pulled both rims off the other (parts) D14, and after attempting my usual trick of breaking the bead with a tractor loader, I knew something was up. This had a steel belted car tire on it, rusted solid to the rim. I dug out my antique tire machine and started working on it. It took two hours to break both beads, then I spent perhaps 2 hours knocking the rust off the inside to see if I could get to the remain metal. Eventually, I was seeing daylight through several spots in the rim. When the bead didn't break loose with the loader, I should have known then that it was a bad use of time to continue. I do everything I can to avoid buying parts, but sometimes, it can be foolish. I'm starting to realize that the other D14 may not even be good parts. I've gotten a few, but it was from the Oregon coast, and I think the salt air really did it in.
The front end is good and I will get one of the spindles off it. One of mine was broken and welded incorrectly (straight up and down) so the camber is wrong.
I'm also attempting to pull the steering wheel. I avoided that last time I refreshed this machine, but the plastic is beyond repair. The early D14s used a solid pin to hold the wheel on, that pin is currently laughing at me. I didn't want to use heat because of fear of damaging the remaining plastic, but that's probably the only thing that will let it come out. These pins AC used drive me crazy. They were a great cost saving maneuver, but made many components horrible to work on. In 59, they eliminated the pins, threaded the shaft and put a nut on the steering wheel like the other vendors. Since the steering shaft u-joints also use these solid steel pins, you can't remove the assembly to get it on a press where they could be driven out. Will have to take a chance with the heat, but getting it hot enough to do any good, will be difficult.
I located a belt pulley and purchased it. It's extravagant because I have not needed a belt pulley for 18 years and even then, it was a grain grinder for feeding the pigs, that would have been powered just fine by a small stationary engine. But I've always wanted one on this machine so I did it. It's on it's way. | | Comments | kevinthefixer 14:18 09/23/17 | That sort of rust inside a rim is usually caused by Slime or similar sealer, but only on tubeless tires, and I'd think your ACs would have tubes. I slimed my front tires on my Case, I got a flat the first weekend I had it, but of course it has tubes so the Slime doesn't eat the rims. My customers get upset when they have to buy a $400 rim for their golf carts because they slimed it last year and now the bead won't seal. | YTSupport 20:45 09/23/17 | It was a tubeless tire but had a tube in it. I didn't even try the other one, I'm pretty sure it's shot too. I'm surprised how much of that tractor is gone. I'm going to end up with a handful of parts when I'm done. It had duals on the rear and all four rims are rotted through. With both tractors, sometimes, it's picking the best of two evils when I decide which part to use. |
|
|
|  07:35 09/24/17
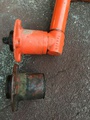 07:35 09/24/17
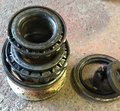 07:35 09/24/17
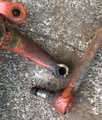 07:35 09/24/17
| 07:35 09/24/17 Spindle ReplacementI chose to remove the spindle from the parts D14 and use it rather than the one on the restoration candidate. You can see from the photo, that whoever welded the lighter orange one, welded it near 90 degrees. The camber is incorrect that way. The dirty one behind it is correct. The donor tie rod end was so rusted that I couldn't tell there was ever a bolt on it, but there was enough left to stop it from coming out. I had to cut it out and slightly cut into the casting at the bottom of the taper. I am going to use it anyway, I keep reminding myself that the tractor has an official max speed of 12 and 4/5ths mph and I don't go above 8 mph with it. Even if the taper spun, there is no danger, not a car, not a truck. Who knows though, I might pop the other casting off and use it on this spindle just for correctness. Such small details can cost another hour or two of work.
I pulled the hub on the donor spindle and at first thought it must be a different part number. The cream painted cap indicates it came from something else and a Series II, III, or IV something else. Looking closer, it was the same part, but a 1/2 inch of it was just gone. It could not hold the grease seal at that rate. So I'll use the hub off the main tractor. Oddly, because they had replaced the dust caps with grease fittings, the bearings from the donor were in great shape (though a massive mess to clean up), unlike the main tractors. I'm going to just replace the grease seal on this side transfer cups and cones to the main tractor's hub and call it good. The grease seals are felt, AC didn't put much effort into machining the surfaces they contact with, both feel almost rough cast. Both spindles had long worn out their respective seals, the donor was using a neoprene style seal and it suffered more than the felt on the shaft surface.
If you look at the tie rod bolt, you can see the extent of damage from rust, it was shot before I took after it with the angle grinder. Heat was the secret again in popping it loose. I still don't have my oxy-acetelyne back so once again I used propane. I gave five minutes heating the joint, then a couple of hard hits with a 36 ounce was sufficient to pop it out. I"m pleased with propane, it's convenient and it's worked every time in this project. I'll probably melt stuff when I get my welding tanks back. I'd never used propane for anything before, this was an old camp light that my dad had bought in the 60s. I borrowed it in the 80s for a camping trip and put a new bottle on it. My nephew was working in my shop and put torch end on the bottle about 10 years ago. It was all I had, so I've used it for this project. Just enough heat but not so much I could damage parts with it. Plus I don't have to go to welding supply to get more. I suppose next I'll use my weed burner to heat rusty parts if this bottle ever runs out (no sign yet after it sitting here all these years). | | Comments | kevinthefixer 14:10 09/24/17 | Little late now, but the trick to popping out a tapered tie rod like that is to leave the spindle mounted solid and smack it, not the tie rod end, so that it squeezes the taper out of the hole like popping a zit. I usually leave the nut on, just loosen it a few turns, so that when I miss with the hand sledge I don't mash the threads. |
|
|
| 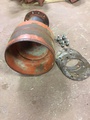 19:56 09/29/17
| 19:56 09/29/17 Belt PulleySince this has turned into a very complete restoration, I decided to get the one thing I've always wanted for completeness on this tractor. A Belt Pulley. I found one for sale and probably paid too much. It will be one third most expensive part of the restoration, but I don't care, even if my kid's inheritance probably does. This came with the shims and everything necessary other than one lock washer and the control arm. I'll fabricate the control arm but getting an original knob for the dash doesn't appear to be possible. I'll be looking at the antique auto producers to find something close, similar to what I had to do with the lighter.
I realize a belt pulley is useless on this tractor. I've ground pig feed before with a rear mount on a Pony, but this mid-mount isn't of value for driving anything I'd actually use. It was totally frivolous. I've wanted one of these for a lot of years, from the first time I saw it in the owner's manual, and I'm tickled. The one difficulty will be sealing it up well. The paper thin gaskets aren't easy to make, I've found not stock that matches what AC used. Perhaps... paper. | | Comments | kevinthefixer 10:36 09/30/17 | Recommend no gasket at all, just a thin even coat of RTV. Won't be at all obvious if you use the orange stuff and don't get carried away like most people do (my 611 has a 1/4" bead of blue all around the PTO housing, and I'm sure one inside also). | YTSupport 06:55 10/01/17 | That may be the right course. It is what I had to do with one of the steering box connections in order to get the bearings tightened sufficiently. | kevinthefixer 13:43 10/01/17 | Another thought I just had while poking around in the workshop; I've a roll of automotive-style masking paper out there. Available at any parts store, inexpensive, thin, designed not to soak up fluids. No idea how it would stand up to long-term exposure to oil, though. | YTSupport 20:24 10/05/17 | I'm liking the RTV idea. It's not a pressurized case particularly. |
|
|
|  20:58 10/07/17
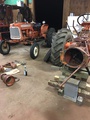 20:58 10/07/17
| 20:38 10/05/17 Cracked BlockI decided to check on the machine shop progress since I really can't start the rebuild without the block and rods. They somehow lost my number. They said "good news and bad news". The head is done, the rods are reconditioned and check out fine. The block is cracked. Aside from the delay, I'm glad to hear it. It finalizes why this engine went south. I was down there in a flash with another block. They will return the other, and I'll see if it's weldable, but that will be for some future project. I would have preferred to have the correct engine number for the tractor, but it's part of a tractor's life to get a different engine occasionally.
Another positive about this is that I had the governor bushing and they will install it along with cam bushings.
Now if this block is cracked (don't know the history since I bought that tractor disassembled) then I'll be looking at a weld or finding another. I do know a fellow with a few. If it turns out to be a weld situation, I won't do it myself. I welded a TO-30 Z129 a few years back (very thin web between the sleeves, they always crack when they overheat) and I didn't have the skill to do a good job and scrapped the block. I'll find a pro welder for that.
All this time was valuable since getting ready for winter and getting the shop ready, hit rather suddenly. The shop and hay barn are nearly painted, firewood is cut but not split, new compressor installed, sand blasting cabinet installed. I wouldn't have got all this done had the block returned a month ago. Silver lining in everything.
Update 10/07/17: I talked with the machine shop this morning and they said they'd press the liners in for me if I send them down. That will save me the work of doing the measurements to mate the best fit of piston to liner, they have the pistons too. Since they are being so nice, I should send the cam and crank down so they test fit those too ;). Seriously, it means I will be hitting the ground running on the assembly when that block gets back.
I shot a picture of the new skat blast cabinet. The installation is done and just have a hole to cut in the shop wall for the dust collection outlet. Also, some of the joints on the new piping for the air, are showing soap bubbles, so I have a bit more work there too. I wish I'd had this when I started this project. Blasting will make such a difference in the final product, but most parts are already primered. (Update: cabinet is now completely functional with external venting out the back of the shop, sand blasting should be more painless than in the past, I'll blast a few parts today that didn't make it on my initial wire brushing and primering. I'm also going to redo the battery box since I was concerned the corrosion wasn't totally removed from some hard to reach places.
I also took a shot at other tractor work I've been filling my down time with. That is the D14s little sister, Kim's D10 joined us in the shop today. Kyle (our son) started it to exercise it today and it gave him a fireworks show. The battery connections were awful. I started to replace the negative cable and one thing leads to the next, we'd removed what was left of the battery box, the battery, the fender, the tool box, and started stripping off all the corrosion that had pitted so much of it. I suggested to Kim tonight that she and Kyle should start the restoration here and now. Those fenders are too valuable to let the corrosion inspired rust go any further. Kyle is still waiting for delivery on his Oliver, so it's a perfect time to start cleaning up the D10. It's unfortunate that it's a different color (Persian Orange #2) because I can't shoot both the D14 and D10 at once. With that blast cabinet, they should catch up to me in two days if they start taking it down. Considering I don't have the engine, they could have it restored before I even get the engine on the D14. | | Comments | kevinthefixer 13:19 10/07/17 | IMHO the best silver lining is that they found it before you did it the hard way. The amount of time you have in this, get it all together, drive it for 4 hours and have it blow up... Good job you had nother block on hand! | YTSupport 20:41 10/07/17 | Now if only that one isn't cracked too. Will have to be reaching for the silver lining then ;). |
|
|
|  | 21:30 10/19/17 Another block crackedThe machine shop called and said the second block was cracked too. I got the message second hand, but the lead had said the crack was in the same place (but didn't relay where). My most trusted AC expert says to ignore any cracks between the cylinders on the G149. He says it won't leak when it's done, but if the crack is in the castings below the cooling gallery, the block is done. I do have another block available, but I'm thinking of running with the original block, crack and all if I find it's in the upper. As I stated before, I had that problem with a Z129 and it wasn't okay. We'll see what happens, waiting for a call from the lead. They did say they would weld it, and machine it, but the cost of machining would be astronomical... I didn't even know a machinist would touch a welded block.
I haven't had much time to work on the tractor because the D10 Series III restoration is heating up. I am feeling the crunch of having several machines awaiting restoration. My experience is that if you don't keep the tractors running and regularly exercised, you will end up with a far more difficult restoration in short order. Fortunately, my son is keeping the D12 running and in use, but soon we'll also have the D17D and D15D here and all of them will need to be kept running. Sometimes too much of a good thing?
Though not on the D14, I have started painting with the new compressor and HVLP gun. The gun is great and the compressor keeps up fine. The bad news is, that buying a cheap compressor for the sand blasting cabinet, was a mistake. I didn't want to put another 1000 in the compressor and bought a harbor freight. It's junk. It has to run continuously to keep up with the cabinet. That aside, I'm going to have to live with it because of the cost, but the cabinet itself is a godsend. Parts are coming out cleaner with less exposure to the dust than I've ever seen. The pieces paint up beautifully. Getting used to the new paint gun is not too bad, but I sometimes feel like grabbing my old pot style gun. Once again, I bought a cheap gun. It's a porter cable that is supposed to be a copy of a binks. It is a bit sticky as if the machine on the needle stop is poor. But it is working, right now just for the D10 parts.
I've done some experimentation with POR-15 to deal with some very nasty corrosion on the D10 (under the Battery). It does appear to seal it up well, but the negative is it's extremely globby and putting finish coats over it, will not smooth it out. I probably should start a blog on the D10.
| | |
|
| 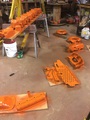 06:16 10/22/17
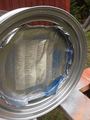 15:07 10/25/17
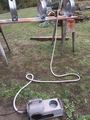 15:07 10/25/17
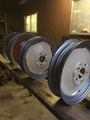 08:02 10/26/17
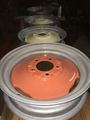 08:02 10/26/17
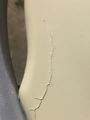 08:03 10/26/17
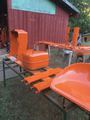 20:44 10/28/17
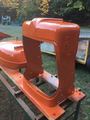 20:44 10/28/17
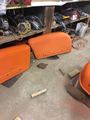 07:11 11/02/17
| 06:16 10/22/17 PaintingSince the cracked blocks issue has the reassembly of the engine on hold, I'm diving into the painting. Since I have two restorations running in the shop, I've got to free up some space. The best way I can figure, is to get as many parts painted and into storage as soon as possible. I had started with the rims but expanded it to all the heavy steel parts and the weights. The weight sets take up a surprising amount of room in the shop. I'm holding off on the sheet metal until I get proficient with the new paint gun. Surprisingly the gun itself is easy to use, the gravity feed is a lot easier than the old siphon pot gun, because I can paint horizontal parts and use right down to the very last of the paint in the tank. But I'm having a lot of trouble establishing the best thinning ratio, and painting too thick as of yet. Yesterday's attempts came out the best yet. I'm using no hardener as the temperature is already down in the high 40s low 50s. The TISCO Persian #1 is making me feel like an expert, but when I have it mixed too thick, that is deceptive. I know the drying will take forever.
I sealed up the leaks on the compressor and that's helping a lot, it seems way to weak for blasting, but for painting, it hardly comes on. I also added several lines to my air system which seem to be helping with moisture. The painting and blasting lines are at the end of about 80 feet of a mixture of black and galvanized piping. I teed in a vertical line with just a drain on it and teed the final line off that, which goes back up to the ceiling before running horizontal and eventually back down to the fittings where I tap the feeds. It works, haven't had any moisture in the paint or the sand. I'm also going to move the compressor outside so it gets the coolest air possible.
Painting has continued and I'm never using brown primer again. Between it and the thinning necessary to use this gravity feed gun, coverage is difficult. Sometimes 2 coats isn't quite enough on rough cast pieces. Since I am clear coating (a first for me), I had hoped to put my time in into the clear coats rather than the color coats. I will probably go back to mixing it a little thicker as I'd started out, but I'd thinned more to hasten drying. I understand that more goes to the pieces and less to overspray around the shop with this HVLP, but I find I run out of paint rather quickly with the little pot. No runs yet which I was concerned about with the thinning. A lot of bugs keep marring the finish though. I dread coming back up to the shop each morning because I don't know who will have embedded themselves ;-). I remember why I like painting after winter starts in earnest. The rims are finally dry enough that I can shoot the aluminum tomorrow. I'll be masking them and hopefully doing only one coat. Then clear coat. I'm hoping the clear coat will keep the scratches down. I can do the D10s rims at the same time and save a little mixing and cleaning later on. I'm finding I spend as much time cleaning the gun as I do painting, nearly anyway. I'm going to take all the rims and tires into Les Schwab in hopes that they can put them on with the least damage to the paint. I still expect a lot of touch up.
Still no word from the machine shop.
Update: I had fun with the aluminum color on the rims. Last night I shot it with my normal gravity feed gun and it was a miserable failure. I was trying something that didn't work. AC painted the silver on the sixties machines directly over the color coat. The cream-hubbed tractors have shown this several times. I thought I'd do as they did. The aluminum paint beaded up like water on car wax, in fact, I could wipe it down like water (fortunately). This morning I went up and lightly sanded, then primered again. The paint went on perfectly. In fact, it looks a lot like the original galvanizing that AC originally used on the rear rims in the 40s. I like the look. Got a couple of runs but I'm going with it. I also used my Turbo HVLP instead of the gravity feed HVLP. Oddly I like it a lot better. It's a Rockler I bought for finishing guitars, and a really cheap unit, poor adjustability, and really mean for wood finishes, but I may use it for the sheet metal. It puts out a better pattern and there is no water hazard with it. If I could afford it, I'd buy a real turbo because it feels much better. The aluminum paint was extremely thin but this unit handled it like a champ. I shot all four rims (D10 and D14) at once, the photo is of one of the D10 rims. After that dries a bit, I will try my hand at the clear coating. I supplied a picture of the cheap little turbo I have, I don't think you'll find anyone using a unit like that to shoot a car or tractor.
Update: I shot clear coat on the rims with a couple of cans for Duplicolor NAPA clear coat I had. I wanted to avoid opening my new can of clear coat until I'm ready to do the tractor itself. The results were okay, except for one of the D10 rims. A 1 1/2 inch crinkle appeared on the front face, so apparently the clear coat reacted with some impurity. I should have sand blasted all the rims rather than sanded them. Never having used clear coat before extensively, I'm displeased with the appearance too. It's impacting the color on the D14 rims which suggests a little murkiness rather than totally clear leaving the Persian 1 color looking a bit more washed out. I'm going to compare to some of the raw painted parts this morning in the light. Possibly I should have opened my higher quality can.
Update: more painting. I started the main sheet metal. I took a hint from the NAPA parts fellow who restores Model Ts. He said use 1K Sealer rather than switch to gray primer. It worked fantastically. The paint flowed perfectly on the parts I hit with the sealer and was awful on the others. The downside was that the sealer is so hot that it tends to dry in the gun and it was spitting chunks that I didn't realize were there. I'm soaking all the gun parts and will clean it out more carefully tomorrow. But the seal definitely improved the finish I'm getting. I painted outside, there was just not enough room in the shop with both D10 and D12 on blocks and all the other parts I'd already painted. As a result, the bugs had a field day, even had a nest of termites popped out behind the shop (VERY unusual, should never happen this time of year). That means I'll be sanding with 1000 grit and buffing a lot of spots. But I'm happy with most of the finish I got. I may try shooting clear on some of the parts tomorrow.
Update: every part that hadn't been primed save the mainframe is now ready for base coat. Tomorrow I'll be shooting coats of Persian #1 all day and hopefully then clear and everything will be done but the tractor itself. It's urgent since there should be two more days of calm sunny warm weather before the rains set in. I'm having to paint outside the shop since there is no room left to paint in there. We were talking about pulling the rear tires, rims and hubs off so that could be done too... since I still have no engine block. I've also split my time with Kim's D10, so the projects have become hopelessly merged for the moment. I have to get it on the road again so I can move it out of the shop to do the final D14 engine build and painting. I did an impulsive thing after having my paint gun shoot chunks. I bought an Accu-spray gun which has disposable tips and pots. It was as cheap as my PSH1 which is considered junk, yet the Accu-spray is considered collision repair shop able. The effort that goes into prep, makes a gun that won't, mean the cost is in the noise, especially with several tractors to do. The problem was that I needed lacquer thinner but had only paint thinner so it didn't get cleaned well enough. But that has happened to me several times even with regular paint. With the Accu-spray, I should be able to shoot multiple colors in one day much more easily.
Update: I shot the rest of the base coat parts and the weather gave me trouble. I had several corrections to make and a few of the parts ended up getting their last coat in the late afternoon. They weren't dry enough to put back in the shop. I decided to take a chance and leave them out, because I'd heard that oil based paint will not be impacted by moisture after it sets up enough. It wasn't enough time and everything left out went to flat orange (see photo of the two fenders, the left one was left outside, right one was inside) on the surfaces that got morning mist. It was a bad idea. Since I'll have to sand everything lightly, do a quick base coat prior to clear coat, it should be okay. The problem I have is the shop is stuffed with parts and not a place to paint now. I'm will need to start concentrating on cleaning my hay barn out, so I can move the painting over to that building.
No progress, getting more shop space has been the priority and it's slow cleaning up, getting more wiring in, dump runs etc. I'm trying to turn my old sandblasting stall into a paint room, the two aren't compatible of course so it's taking while, the hay barn was just too full with all my deceased parents junk. It will be 20 or 30 dump runs to get rid of it. So cleaning the sand blasting garage makes more sense. Then I'll have to plumb the air into there and put new a new dryer in the line. We also got my sons Oliver 1950 FWA here now and it's giving some problems with Governor and now even starting with the temps hovering around 32 plus the 3pt needs work that I have to do. I did box up all the carb parts and kit and brought them down to the house. If I get the carb rebuilt this week, that's about the best I could hope for. I was also thinking about dragging the wiring and dash down and doing all the wiring and gauge installation in the house. That would be another great step forward. Finally got through to the machine shop and they want me to make a trip to view the block cracks so I don't come back and complain that they picked the wrong one to surface. It does concern me to have so much effort and money into a tractor, and leave the cracks as is, potentially fighting head gasket leaks every time I get it too hot. Since they won't be structural, I may just experiment with JB Weld. I've done it before successfully on a B and it's still holding after 20 years without leakage. It would just be insurance since I want to use this tractor regularly and potentially hard. I'm well aware that that is a cardinal sin to use.
Update: after a lot of trouble with temperature, the old paint gun and viscosity, I finally got the paint working well. I had to use acetone as a thinner with a bit of mineral spirits. Then using this new Accuspray One gun, the results are excellent, even at 50 degrees and high humidity. For the first time, I had an atomizing paint and gun, it's drying is a little slower than it would be in summer, but the acetone sped it way up. The gun is great, as advertised, I can get it clean with about 2 tablespoons of lacquer thinner. I was also thinking of trying naptha too, but I had heard it could cut down on the final gloss with alkyd paints. | | Comments | kevinthefixer 19:18 10/24/17 | Don't try to get the bugs out while the paint is wet, let it dry and harden, then just run over them with a bit of fine sandpaper. Then shoot your clear after the bugs all freeze. | YTSupport 14:49 10/25/17 | Yep, good advice. The bug damage was minimal as a result. I'm thinking they may not go away this year, it was still a nice balmy day. | kevinthefixer 19:17 10/25/17 | Well we might not freeze ours, but we haven't had too much trouble with them all summer--too hot and dry. Only a few flies, I blame them on the horses in the neighborhood. | YTSupport 08:25 10/26/17 | We had a lot more flies when we had horses and cows, but I have a few acres of peat bog at the front of the property, mosquitos, crane flies and other small water breeding insects are the problem. I think they are attracted to the AC Orange. They've left the cream parts for the D10 alone. | kevinthefixer 18:07 11/06/17 | Depending on where the crack(s) might be, you might consider the drill/tap/plug, drill/tap/plug repair also, possibly in conjunction with JB Weld. Best epoxy made, but block repair is asking a bit much of it. | YTSupport 07:20 11/12/17 | I'll see when I get it back. I really want to avoid a repair that will cause more machining. If I were going to do that, I'd probably first go pick up another block and try again. The crack is non-structural (though I haven't actually seen it yet). I'm a bit demoralized about it anyway since so much work has gone into this machine thus far. I've even toyed with the idea of fitting a modern diesel on it for fun, just toyed so far. I'm going to try the easy way first though, the tractor will never be sold anyway. |
|
|
| 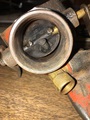 07:46 11/16/17
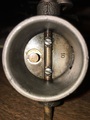 07:46 11/16/17
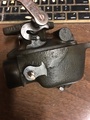 07:46 11/16/17
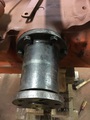 08:00 11/16/17
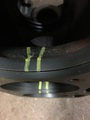 19:28 11/21/17
| 19:04 11/14/17 New Engine BlockWhen I was talking to Kevin about epoxies and the crack in the two blocks I already had magnafluxed, I started to get cold feet. Putting this together with what I have in it for new parts, shouldn't' be dependent on a tube of epoxy. I located and bought another G149 block which the person is reasonably sure it's not cracked. I'm having the shop send me back everything they have now, and will get this one in for magnafluxing when it arrives. It's coming with my D17D and D15D within a week or so (BTW, the D15 Diesel turns out to run like a top, I was expecting to rebuild it). Very excited about that.
I went to assemble the carb today and realized, it was still too dirty. I dumped out my simple green from the ultrasonic and pour in about 40 / 60 pinesol and water. Ran that for an hour at 50 degrees centigrade and it is already looking nearly as good as the new MS Carb I saw yesterday on one of the YT Salesman's desk. From what I ready, people normally soak carbs in pinesol for several days, so I'll put it back in the US bath tomorrow for a couple of more hours, but right now, I'm impressed with pinesol. I don't think simple green competes well with it in the ultrasonic.
Update: some photos of the pinesol before and after. The first photo was the "clean" carb after running it through the ultrasonic with simple green for a day. The carb was not exactly clean. The second is after running two hours in the ultrasonic with no manual cleaning (no wiping down). The difference is astounding. After I blew it out and wiped it down, it looks like new.
I also reinstalled the belt pulley with a thin sealer. I'm comfortable that it won't leak, but I am concerned that when (not if) I need to remove it to replace the main clutch shaft seal, getting the thin shims completely clean, may represent a significant task. I used a purple permatex as my gold colored stuff had gone bad after sitting in the can for so many years.
Update: Though the new block is on it's way, I got the other two back today. The cracks are in the webbing between the cylinders (3 on one block and 2 on the other). They don't extent to the head gasket mating surface and I believe they could be welded with NI-99 nickel and ground out without compromising the sleeve mating surface. The weld would be below the mating surfaces and far below flange the sleeves fit into. Hopefully the new block will have no cracks and will be the one I use in this restoration, but I think I'm going to try to weld the one with only two cracks. This rod is supposed to be machinable, though I don't think the machine shop will touch any weld. (Edit: I also found Easyweld Tig Wire which may be a better choice, may not require preheat or slow cooling, which is very difficult with a block). If I can drill the head of the cracks, vee the webbing and weld it, the sleeves should fit in and there should be sufficient untouched mating surface to avoid fluid mixing. Whether I'm willing to bet another rebuild kit on this or not, I haven't made up my mind. The welding shop offered me some free rods to try it out today, so I may try it on the worse of the two blocks, practice up and then go for it. I should be able to test it with the numerous sleeves I have laying around. The cracks are yellow outlined in the photo, and the one close up is representative of all five cracks in both blocks. It's clear why Bob VanderPloeg (a serious AC expert), told me these blocks would seal and work. When torqued, the head would keep these at bay. This must have been a very common AC problem. The webbing is way too thin, similar to Continentals blocks, only they would crack all the way to the mating surface. But I already bought the new block so I'll put my money on it for now, these will be a great future experiment and chance to improve my welding. | | Comments | kevinthefixer 17:48 11/18/17 | IIRC gasoline will take off the purple Permatex, that is the #3H in the bruxh can. Certainly carb cleaner can, either dip or spray, or brake cleaner. Note that spray carb cleaner isn't what it used to be, I've been using brake cleaner instead for years now. | YTSupport 11:11 11/19/17 | Mineral Spirits cut through it pretty well too. Had to wipe the outside of the case off where I got a bit on it. |
|
|
| 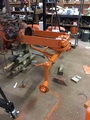 19:42 12/13/17
| 19:42 12/13/17 Last entry here (really)I'm reassembling the tractor to some degree, and it makes not sense to continue with the cleanup blog. I have to wait for the new block to get here and then potentially a month or more to get it tanked and magnafluxed, so the front end went back on tonight, and tomorrow it's going back on it's front tires. Then I'll block it up and remove all the wheels and tires to finish sanding, degreasing and painting the main frame. My plan is to wire it, paint it and reassemble everything that can go on prior to the engine rebuild. Then will move it to storage and begin more serious restoration of the D10 and D12 (they will play nicely in the same shop given their size and needing to both be the same colors. When the D14 engine is done, then I'll haul the rest back into the shop and finish it.
One thing that's a shame, is that it's gone too long to clear coat the parts I finished painting, so all will require roughing and recoating with base color. That's good anyway, since I'll be doing all the work in the shop instead of outside. Should be able to bring everything up to a reasonable temperature and do it well. I was thinking tonight that one thing I'd like to try, is clear coating over the decals. I've never done that before, and since I use the mylar sheets, I've never been happy with the results as the mylar covered portion ages at a different rate. Clear coating over them, should solve that. Even if I sprung for the die cut decals, there would still be a texture difference between lettering and the painted areas around them.
Part of the reason I need it out of the shop, is the wood stove is all back together, and it's currently sitting inches from the stove, moving it is a necessity to be able to stand being in the shop. It's day after day of freezing weather right now, and the cold makes working out there no fun.
Another project related to the D14, is fabrication of the battery hold down. That is something I've never seen on any D14 or D15. They are always gone it seems. I'll be fabricating it from the parts manual drawings but I should be able to get close.
The new blog will be "D14 Engine Rebuild - Reassembly". | | Comments | kevinthefixer 18:06 12/15/17 | Recommend you do a trial run with a decal you don't care about before you start squirting strong organic solvents on top of decals you do. Given newer paint technology, I don't know anyone who can keep track of what paints are safe with which decals. Also, I wouldn't count on the aging effect you're looking for, much of it is due to sun damage (we know about that here in AZ). The clearcoat might help that if it has a UV filter, but not eliminate it. Might protect the decals, though. | YTSupport 17:59 12/17/17 | This is all Alkyd oil based. Probably not a bad idea to do a test. I have two complete sets of Farmall H and Super C decals I can play with. We don't have much to worry about with sun damage here ;-). |
|
|
| 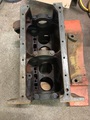 19:11 01/16/18
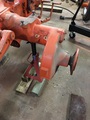 19:11 01/16/18
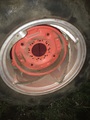 19:11 01/16/18
| 19:11 01/16/18 Another entryI am still tearing down so I thought I'd post another entry, plus I got my new block. It looks better than either of the other two and I can't see any cracks. I'm thinking about not having it tanked just because of the cost, but if I don't I'll be just hoping it doesn't have hairline cracks like the others. I also pulled one of the tire, rim and hub assemblies off tonight in preparation to clean, sand and paint the main frame. It looked good, some weeping but no leaks, so I'm not pulling the rear axles out. The rim looks okay, but I have to decide if I want to go for a dismount and weld up new metal around the stem. It's not great looking, but the expense of draining and dismounting, remounting and filling does concern me. Then again, with what I have in this so far, where do you stop and say enough's enough. | | |
|
| 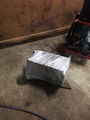 19:32 02/08/18
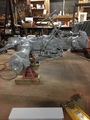 19:32 02/08/18
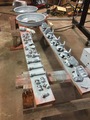 19:32 02/08/18
| 19:32 02/08/18 Block Back, priming doneI got the block back, no cracks! Here is it still wrapped in plastic, will put it on the engine stand tomorrow and get going with the new blog.
I also primed the rest of the tractor and plan to shoot it this weekend with color and clear. Will have to sand all the currently base-coated parts and shoot them at the same time. That should be a long day. The temperature is hovering around 50 and I am concerned about using acetone to cut, which is critical when it's cold (it has worked great on everything I've painted this winter, dry time was quite quick), but I read that it dulls the finish. Since the clear is providing the shine, that may not be a problem, but it's a new adventure this time. I shot my B during very cold weather and aside from a orange peel that needed a lot of rub out, the finish has been great, still looks like new after 20 years. So I'm not too worried about the cold, but I don't want to spend a lot of time rubbing out.
The 3M accuspray system worked fantastically. I'd used one of the disposable tips for about 8 jobs and they are supposed to last for 5. I popped on a new tip and had a new gun. At about 5 bucks per tip, it's economical if you want a quality job. I never could clean my gun good enough to guarantee a good finish on the next job. It also works as advertised, takes about 2 or 3 teaspoons of lacquer thinner to clean. It also shoots upside down which is very nice when you are shooting the bottom side.
With winter weather keeping me trapped at the computer, it feels great to get something done. Getting the garden ready for spring has also been a outdoor draw. The temps are so high that we are planning to plant early. In fact, our overwinter vegetables are growing already. We have onions, garlic, and cilantro that may be ready to harvest in a few weeks. Very odd. | | |
|
| 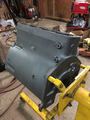 19:14 02/09/18
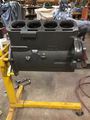 19:14 02/09/18
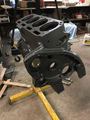 19:14 02/09/18
| 19:14 02/09/18 The Block unwrappedCould not be happier with how the block looks. The machine shop kissed the important surfaces enough to smooth them out. Put it on the stand tonight. | | |
|
| 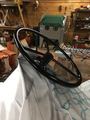 19:09 02/13/18
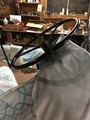 19:09 02/13/18
| 19:09 02/13/18 Steering WheelJust filling time until my shop roof is done and I can safely paint the final coats (plus hoping for warmer weather), I fixed up the steering wheel. It had large cracks at every spoke. I filled the cracks with epoxy and built-up the connection points to the spokes, then filed and sanded it all down. It doesn't look new, but to the casual observer, it looks okay. I should have replaced the steering wheel, but getting the pin out (the early D14s and D17s used pins to hold the steering wheel on rather than the bolt on style that came out in 59 and was already on the D10 and D12, horrible idea as those pins don't come out, I figured it was cut the wheel off and drill the pins to put a new one on. Didn't want to do that.). It may come apart, and if so, at that time, I'll buy a new one and go through the pain. I'll buff the black paint to a semi-gloss except on the spokes. That will hide the sanding marks.
After uploading the photos, I realized they are so fuzzy that you can't tell, there is a nice gloss on it. It was they way I exported the photos, the steering wheel looks pretty good.
BTW, I'm putting a black spinner on it in the hopes that it might torque the wheel less and possibly allow the epoxy to hold better. Without power steering, it needs it anyway. | | |
|
| |
|
| Return to Journal list |
|
What are Project Journals?
Project Journals are a place where YT Community members can document their tractor and farm projects. Each journal created, can have many photos and accompanying text entries. You can also enable comments to allow other members of the YT Community to comment on your journal. If you do enable comments, it is up to you to moderate what people enter in your journal according to the site policy of Yesterdays Tractors. Journals may also be used as photo posting area, to post your photos of your farm, tractors and related photo topics. If you would like to create a journal, just be sure you are logged in to the Classic View of the forums, and a link will appear to do so when you next come to this page. . |
Home
| Forums
Today's Featured Article -
Grain Threshing in the Early 40's - by Jerry D. Coleman. How many of you can sit there and say that you have plowed with a mule? Well I would say not many, but maybe a few. This story is about the day my Grandfather Brown (true name) decided along with my parents to purchase a new Ford tractor. It wasn't really new except to us. The year was about 1967 and my father found a good used Ford 601 tractor to use on the farm instead of "Bob", our old mule. Now my grandfather had had this mule since the mid 40's and he was getting some age on him. S
... [Read Article]
Latest Ad:
1964 I-H 140 tractor with cultivators and sidedresser. Starts and runs good. Asking 2650. CALL RON AT 502-319-1952
[More Ads]
Copyright © 1997-2025 Yesterday's Tractor Co. All Rights Reserved. Reproduction of any part of this website, including design and content, without written permission is strictly prohibited. Trade Marks and Trade Names contained and used in this Website are those of others, and are used in this Website in a descriptive sense to refer to the products of others. Use of this Web site constitutes acceptance of our User Agreement and Privacy Policy TRADEMARK DISCLAIMER: Tradenames and Trademarks referred to within Yesterday's Tractor Co. products and within the Yesterday's Tractor Co. websites are the property of their respective trademark holders. None of these trademark holders are affiliated with Yesterday's Tractor Co., our products, or our website nor are we sponsored by them. John Deere and its logos are the registered trademarks of the John Deere Corporation. Agco, Agco Allis, White, Massey Ferguson and their logos are the registered trademarks of AGCO Corporation. Case, Case-IH, Farmall, International Harvester, New Holland and their logos are registered trademarks of CNH Global N.V. Yesterday's Tractors - Antique Tractor HeadquartersWebsite Accessibility Policy |
|