| |
Project Journal - D14 Rebuild - Re-assembly |
Handle: |
YTSupport |
|
Project Name: |
D14 Rebuild - Re-assembly |
|
Tractor: |
AC D14 |
|
Started: |
16:11 02/20/18 |
|
Updated: |
07:25 05/26/18 |
|
|
Expand/Contract all Journal Entries Show newest journal entry on top |
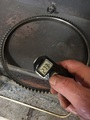 16:35 02/20/18
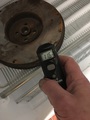 16:35 02/20/18
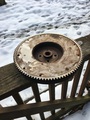 16:35 02/20/18
| 16:35 02/20/18 Flywheel and Ring GearThe last three blogs I did on this ran long and very slowly. I left the clean-up blog because the everything is cleaned, primed and many pieces even have base coats, the block is tanked and on the engine stand, even the carb is already rebuilt and reassembled. I figured it was time to open this one up.
Today I put the ring gear on. I was sad to see that my freshly ground flywheel was rusted, but it was to be expected given the months all the parts have set. I cleaned up the ring gear mating surfaces first. It has a cutout on it's back side that mates to a machined protrusion going around the flywheel, I didn't want any dirt in there and also cleaned off the light surface rust with 1000 grit, then took naptha and cleaned up the surfaces to make sure no dust or particles were left. Then the flywheel went in the freezer (set to 0 degrees) and I waited till it reached about 8 degrees, then tossed the ring gear in the oven on broil (500). I'd put the ring gear on the wood stove while waiting for the flywheel to cool, and it was about 270 when I put it in. With the temperature outside at 25 degrees, I didn't have to work quite as fast as I might have. I placed the flywheel face up on my deck rail, took the ring gear out of the oven with a couple of hot pads, and dropped it on. It really just dropped on. I had a punch handy just in case, but it wasn't necessary, it's seated really well with no visual runout (I will measure it later). It always amazes me how well expanding a ring gear works given how hard it was to knock off there. The final temperatures that worked well, were about 10 degrees on the flywheel and 400 on the ring gear.
After that, I buffed the rust off the surface with and sprayed it down with LPS so it wouldn't rust further since it will sit for a good time until the engine and painting is all complete.
Sometime in the next week, the camshaft and sleeves will be going in. The shop roof has to be replaced first, and the snow is holding things up. | | Comments | kevinthefixer 08:50 02/24/18 | That's as clean an install as it gets! Given the care you're putting into this, your grandkids will be proud of the job you did long after you're gone. | YTSupport 16:57 02/25/18 | Yep, my son is planning to keep all the tractors for good. They may as well last another 100 years, which they will without having a hard use they've all had. That ring gear install tickled me, it just bounced onto the flywheel with the heat differential. I should have cooled the sleeves as they too would have slipped in just by hand, they were warm and the block was frozen. |
|
|
| 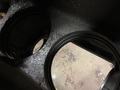 18:56 02/24/18
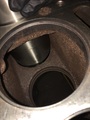 18:56 02/24/18
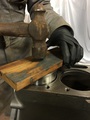 18:56 02/24/18
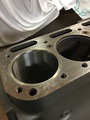 18:56 02/24/18
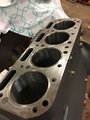 18:56 02/24/18
| 18:56 02/24/18 SleevesHad a few spare moments so my son and I decided to install the sleeves. Used dish soap on the o-rings because that is all I had. These Tisco o-rings probably would have been fine with petroleum of some sort, to provide lube. It may not have been necessary anyway, since these sleeves come with lube on them. I tapped them in very gently, ignore that the hammer is a 36 ounce, I barely tapped them and they seated nicely. The wood I used is epay. I had scraps laying around and prefer it's hardness, no sawdust can come loose from it, no chipping or cracking, yet it still doesn't mar the surface of whatever you are tapping in. I've done this in the past by myself, it's so much nice to put those o-rings in with two sets of hands, one from underneath and one from the top.
We will do the cam tomorrow night. The new roof is on the shop and it's so nice to have a dry place to work. | | Comments | kevinthefixer 18:42 02/27/18 | For most automotive applications, and notably Mazda rotary motors with half a million o-ring seals, they recommend petroleum jelly as assembly lube for o-rings. Slick enough yet stays in place, and apparently it won't eat standard o-ring rubber. | YTSupport 04:47 02/28/18 | That's an engine I don't think I'd try to rebuild. That's interesting since it is petroleum based. I've heard the soap can be a problem with foaming in either oil or coolant. I was very sparing with it. Just drop on the tip of my finger for each set of o-rings. The Tisco sleeves come with a lubricant on the lower portion of the sleeve and wrapped in wax paper to protect it. |
|
|
| 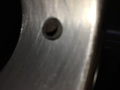 19:01 02/25/18
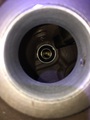 19:01 02/25/18
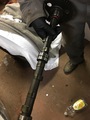 19:01 02/25/18
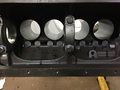 19:01 02/25/18
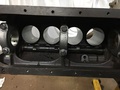 19:01 02/25/18
| 19:01 02/25/18 Camshaft installPut the Tappets and Cam in tonight, or I should say, put the cam in, pulled it out, put the tappets in, then put the cam in again. The only notable thing is to remember and verify that the bushings are lined up with the oil holes, or the engine will run for about a minute and a half before itself. We used the mixture of STP and 90 weight for assembly oil, half and half. As a airplane mechanic, my brother explained that it's a regulation because an engine may sit for a time after the assembly is done, that mixture apparently stays where it's put pretty well and if the engine remains crated for a couple of months, it won't destroy itself when it's finally started.
The new parts look just great. I would have done the oil pump at the same time, but the engine stand blocks access to the rear of the engine. I'll put the pump on when it's time to put the flywheel and clutch on. I wanted to pump the cam and passages full of oil anyway, and that should be just before we put it back on the tractor. Tomorrow, hopefully the crank and mains. I thought I might plastigage them just to verify that the new crank will actually take standard mains. It should of course, but Just trusting it would is probably poor practice.
Afterthought, there is one other thing to verify before putting the cam in. That is that there is a pin on back side that drives the oil pump. Just need to check that it's there on return from the machine shop, or if you pick up a new one. | | |
|
| 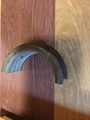 14:34 02/27/18
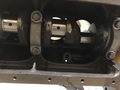 14:34 02/27/18
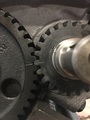 14:34 02/27/18
| 14:34 02/27/18 Crank installToday we took a few minutes and installed the crankshaft. The only notable things are that for this engine, the rear main bearing has shoulders on it (see the old one I shot just for an example). The shoulders provide the forward and backward clearance so you don't have too much slop. On this model, it's 4 to 8 thousandths of an inch that is considered acceptable end play. That is a tight enough fit that when you first drop the crank into the new bearings, the back may not fit in. You have to turn the cam and crank gear just a hair so the crankshaft can slide backward and go into that last bearing. The angled gear teeth will hang it up just enough that it won't slide in unless you do.
I used 90 Ft Lbs torque to hold the caps down, but I may check it to 95. The factory manual says 80 Ft Lbs, but the I and T specifies 90-95. The other manuals that cover this block (D15, D10, and D12) also say 90-95 pounds, so that is what I went with. I made one mistake and got some assembly oil down in the threads of the center cap. My son got overzealous with the oil. I'm certain it hurt my ability to torque it accurately, so I may pull that one out, wick out any remaining oil and clean that bolt thoroughly. It just makes me a bit uncomfortable with such an important torque spec. Should have done it then, but I got rushed. I had to use a manual torque wrench because I misplaced my ratcheting one somewhere, I don't trust those old bending wrenches, they are too hard to read accurately.
The other very important issue is the timing marks. The cam and crank gears lined up as in the photo.
I'm really taking my time rebuilding this thing, before because of machine shop holdups, but now just because I do want each step to be perfect, very clean, and I want it to be instructive to my son. If we put the entire thing together in one day, it would be too much of a blur for him. I fully expect he will be doing the work on some of the machines waiting for rebuilds. Eventually his Oliver GM 453 will need rebuilding and I'd like him to do either the D17D or the D15D (both smoke so badly you have to run out of the barn when you shut them off or you can't breathe) so he can work with the tolerances of a diesel before he takes on the big guy. But doing the job slowly is restful and enjoyable. I also like this engine. Building B and C engines as I have in the past involve shimming the bearings and that process felt like voodoo to me.
Another inaccuracy in the factory manual (D14) is that their photo of the crank installation shows shims. There are none on a G149. By the later manuals (D10, D12 and D15), they had corrected that.
Spinning this crank after the installation feels great, smooth as can be. | | Comments | kevinthefixer 18:49 02/27/18 | How did the Plastigage check go? It's great stuff and works better than Sominex. It's addictive, though. Keep up the good work! | YTSupport 04:53 02/28/18 | Best experience I've had. I think that is because I bought a new crank guaranteed to work with standard bearings. I've always taken the cranks to a machine shop and I would attribute problems I've had to less than perfect finish work on the cranks. I'm going to try that again though by getting one of these extras ground at this place I found in Tacoma. I'd like to have a spare engine since I have 3 tractors that can use this engine model. |
|
|
| 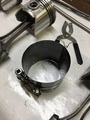 19:08 03/04/18
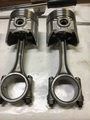 19:08 03/04/18
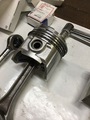 19:08 03/04/18
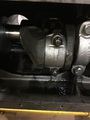 19:08 03/04/18
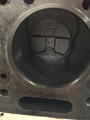 19:08 03/04/18
| 20:10 03/03/18 Pistons, Rings and RodsI said I'd be putting the pistons in, but I ran into a couple of snags. The problem is that I'm not comfortable with the fit of the wrist pins, they seem too tight. I had an engine freeze up once on a rebuild due to the pins being too tight in the piston. When it heated up, one cylinder froze. I came down and found the specs (.8133-.8135) so I'll be check that in the morning. If it is too tight, I'll run down to the airport as my brother has a ream. It appears a 13/16s ream runs 160 to 225 online. Ring end gap checked out at .011, right between the spec of .007 and .017, no filing to do, that's good. Photos of the install maybe tomorrow night.
Update: I took the pistons and pins in and we measured them once more. It turns out that the .0004-.0007 clearance is just a tight fit and I was wrong ;-). They were correct out of the box. He showed me some new pistons and pins on a Lycoming and felt these were plenty loose. I think I'm just paranoid about it because of the rebuild that went bad. It was a good time though, I acted as the gopher while he did maintenance on an Apache twin. It is an eye-opener when you are used to mechanic work on a truck or tractor. Every bolt has to be done correctly including the length and positioning of the cotter keys. If I had life to do over again, I think I would have tried for a teenage job at an airport mechanics facility, it would have prepared me to do much more exacting work. I was too busy wrenching on motorcycles and cars and developing sloppy habits.
I did the wrist pin, rings and actually installed in one cylinder. The operation is smooth and feels great. The torque values I used were 35 on the wrist pin clamp and 40 on the bearing cap nuts. I'm going to reuse the pal nuts just because I don't have new ones. The only mistake I made was not putting the bearing in before slipping the piston and rod into the cylinder. It's a lot harder to do it that way, and since your view is poor, it concerns me that cleanliness suffers doing it that way.
It's nice taking this very slow, having to work on the site and take care of the farm, I let this machine sit for so many years thinking if I couldn't work on it continuously, I may as well not start it. But just taking a a few minutes to a couple of hours a day is getting the job done, almost better I think. Hopefully then engine will be done by the time we get some painting weather. I'm simultaneously running a test of the decals with Tisco clear coat, I took my old IB hood and put a Farmall decal on it (it has to be stripped anyway) over a few coats of cream base. I thought I'd see how the decals looked under the clear. Unfortunately, it's too cold to shoot the clear. | | |
|
| 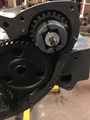 19:20 03/10/18
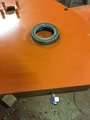 20:23 03/12/18
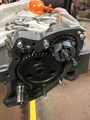 20:25 03/13/18
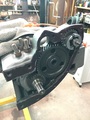 19:30 03/16/18
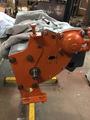 19:30 03/16/18
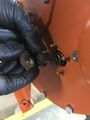 19:30 03/16/18
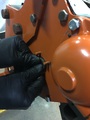 19:30 03/16/18
 19:30 03/16/18
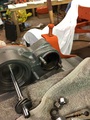 19:30 03/16/18
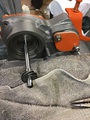 19:30 03/16/18
| 19:20 03/10/18 Front Engine CoverI had the wind let out of my sails once more. I had purchased the new governor from YT's stock because all of mine have worn gears (badly, some photos in the cleanup blog). I also picked up an AGCO-only bushing for the front of the governor cover. I was already to assemble the governor, distributor drive housing, and front engine cover and went to pull the old bushing. Fortunately, I fit the bushing to the front of the governor shaft, the shaft swims in it, way oversized, probably a 32nds inch clearance when it's supposed to be .002. I doubled checked and it is the right part number on their books, but not in the old parts manuals. I'm guessing the early D14s/G-149 engines, had a different governor shaft, and even though we are selling the original style, AGCO is selling a larger bushing for a different governor, likely a later D15, D10, D12 style. Every original governor shaft I have is totally wrong for the AGCO part. Frankly, the one on the second cover I have, fits without too much slop, but I'm still a bit troubled about not being able to put in a new bushing since the other two on the governor are perfect. I stopped and have spent a couple of days ruminating on whether to go with the cover and bushing I have, or make one out of brass. I'm not a top notch machinist, and I could have my brother do it on his more pro equipment, but hate always having to go to big brother for the hard stuff. It's a trivial part with a substantive lathe. My mini-lathe is not that solid, so there is a good chance, the one I make will have about the same clearance as the old one in my spare governor cover. So just waiting until I make up my mind. The governor cover can come off after the engine is installed, so going with the old one isn't as bad as it sounds. I actually keep worrying that maybe I'm just lazy and using it as an excuse, this engine could be done in a day if I just moved forward with what I have and the old cover feels quite good.
The job is to put the front crankshaft seal in, slip the cover on and bolt the cover on loosely after putting some shellac (I'll be using purple sealer) on the gasket both sides, spin the crank a bit with the bottom leveled to the pan surfaces on the side of the crank. When it seems centered enough, bolt on the front plate, power steering cover, and governor cover and cinch them to whatever the torque is for 5/16ths bolts (I'm showing 6 to 8 ft lbs, seems low). Everything has to be centered very well because it's a poor design which integrates the front engine mount into the holding force on the front plate. If it leaks, you have to pull the front end to fix it.
Update: Deleted yesterdays gripe, not enough space to waste it that way. I went to the shop to work for a couple of hours, but the D12 worked it's way in front of my work. Had to clean out the float bowl, air cleaner, and get the fuel flowing smoothly again, as my son wanted to use it and it wouldn't run. The oil bath air cleaner was full of some sort of thick ooze and water, nothing else, then had to put the screen mesh back on the bottom where the previous owner somehow had it all mangled. Sediment bowl had about 3/4 inch of rust in it, doesn't bode well for the tank condition. Anyway, by the time I got back to the rebuild, all I got done was cut off a new 5/16s pan stud and stake that in place (and clean up the threads, then glue and press in the new seal. I used the purple sealer. Should be ready to bolt up the front cover, maybe tomorrow night. The paint is dull because I cleaned it all up with lacquer thinner after getting the sealer all over it. It's all getting re-re-painted before I clear coat anyway.
Update 2: Tonight I did get out and meant to put the front cover on, but I had test all the bolts I'd prepared for the installation and realized, almost all of them were shot. I had ordered and had on hand 5/16s in 3/4 and 1 inch so I thread chased all the bolt holes and put new bolts in them. Plus the large engine mount bolts, which have to go on with front cover, or it won't seal correctly, also were badly stripped. I had to run them through a die and use a tap on those wholes. This wasn't the original block if you recall, so I'd never checked any of the bolt holes on it. Needless to say, the front cover didn't go on, and I put probably 2 hours into this process. When you figure how long a restoration takes, this is the sort of thing that, if you are doing the job right, will make the job take many more hours than planned. But it's looking good, and I know when I work on it, it will be like working on a new tractor rather than a very old one. So much for using the original bolts, but it will feel like a complete job.
Update 3: Finished the front cover and governor. I'm showing the relief valve order of install with the springs and thrust plate. Inside is the ball that fits into the camshaft to act as the valve. I show pushing the plate in (which requires a lot to tension, but actually when you install it, it's best to put the small square cover in place, push it on so you can get a couple of nuts on it, then position the plate to fit in it's holder, then tighten those enough to get some clearance to put the two other nuts on with their lock washers. Then remove the original two and put their locks on them too. Then tighten the whole thing down. It's a job for two people because the plate will fly out with a vengeances.
The last two photos are something I'm concerned about. That is the power steering mount and I don't have power steering. The block is different having that protrusion sticking out to mate with the pump. The cover for the later blocks may have been different. The last picture shows the plate in place, but it doesn't have a lot of tension on it. I couldn't do that given the plate will bend with a lot of torque on it. I may have to make a much heavier-stock version of the plate to keep from having oil seepage around that circular protrusion.
Well, this section is done. Tomorrow I will put on the distributor housing and maybe start on the head. I can't mount the engine up until I paint the tractor, so I am going to have to cut over to painting again. That means a day lost to making the shop clean again (still a mess from the reroofing a few weeks back). I have to paint the main frame in order to put the wheels and rims back on (which also have to be painted. Right now, my plan is to paint and clear coat the rear end up to the torque tube, then put the tires on so I can safely mount the engine, then finish the engine assembly and paint the front half. It's sometimes tough to figure out the best order to do things. | | Comments | kevinthefixer 18:21 03/11/18 | Do you have the exact dimensions of the bushing? Maybe something from some other machine might work. | YTSupport 20:21 03/11/18 | I didn't take them yet. I'm really thinking the fit is good enough on the old bushing, the tractor that cover came off, was not worked as hard even though the tractor itself was a rust bucket. I'm using a lot of parts off it. I balked at putting it together today too, just fit parts up and planned, that's procrastination that comes with being unsure of a job. | kevinthefixer 19:08 03/14/18 | On the subject of bolts, anywhere you expect a lot of stress (thinking of engine mounts), I recommend grade 8, even if AC originally used gr5. The standard grade 5 bolts we buy today, well, we refer to them as "butter bolts". They are not nearly as strong as the old ones. | YTSupport 07:11 03/16/18 | When I was buying capscrews and nuts, I didn't worry too much. The 5/16s on this engine probably makes that okay, I can think of any that have excessive stress. I'm using all originals on the ones that do. I went to hot rod shops for the few that do take a lot of abuse. Got some very nice looking stud bolts/nuts for the manifold from one. | kevinthefixer 19:19 03/17/18 | Too bad we didn't notice that protrusion when the block was empty, we could have simply pulled the 2 studs and ground the surface flat with a body grinder. But it looks like you have plenty of stud there, so probably a piece of 1/4 plate should do. I would also build up a bit of weld on the far side of each stud hole, about the same thickness as your protrusion, to minimize the bowing effect. | YTSupport 08:04 03/18/18 | I've got 1/4 and even 3/8s stock. Seems an interesting approach might be to bore on my brother mill so it inlays. and still seats on that surface. Could even use an o-ring to seal then by making trough around the outer edge. That would be sophisticated. But just a flat surface would do fine too. |
|
|
| 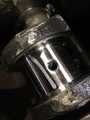 17:52 03/21/18
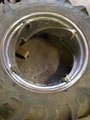 20:14 03/26/18
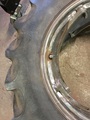 20:14 03/26/18
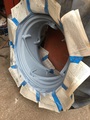 20:05 03/28/18
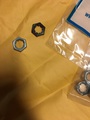 20:05 03/28/18
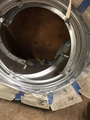 20:06 03/29/18
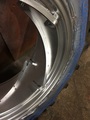 20:06 03/29/18
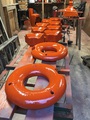 21:10 04/03/18
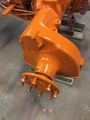 21:10 04/03/18
| 20:58 03/20/18 Crank jammedI'm rewriting this to shorten it and make it less rambling.
After the front cover was on, when I'd try to turn it over, it was feeling way too stiff. I measured the endplay of the crank by putting feeler gauges between the front and the back of the rear thrust main bearing. There was less than the allowable. I couldn't get a .001 in on one side without prying forward on the crank. It's supposed to have space there because there are longitudinal movement when the engine runs, no matter how slight. Something was jamming the crank.
I first plastigauged the rod bearings since I hadn't done that, they checked out perfectly (photo to left shows roughly .003 if I recall, the mains were plastigauged last time). After all the rod bearings were off and the pistons pushed as far up the sleeves as possible, it still wouldn't release to get some space between thrust main and crank. I realized I'd have to pull the crank pulley and front cover off (and get new seal and gaskets).
After disassembly, the problem immediately became apparent. With the front cover off, I had an easy .002 in front of the thrust surface, and .004 behind it. That is in the allowable range the crank should be able to move back and forth (it's supposed to be .004 to .008 total end play). The crank spun very smoothly and freely. I got to looking at the front seal and one side of it was smashed out of round. I reassembled all the bearings (this time using a light moly based Honda motor oil) and it spins freely (as freely as new rings allow). Unbelievably, that little seal had been holding the crank shaft back due to being misaligned.
The wimpy little seal should not have been able to do that, so more is in play here. At present, I'm thinking that front cover is not centering itself well enough on this block. I have another, and after things are all cleaned up, I'm going to test fit it and get another front seal. We don't have a seal or another front cover gasket at the warehouse, so I'll be waiting now. Since I'm not a customer, I'll just wait for a stock order, meaning I'll have a week to work on other parts. Need to clean and paint the rear rims anyway, so I can wait.
It appears I will have lost a bit more than 2 hours on this, hopefully that won't increase as I try to make sure it doesn't happen again. (update: I cleaned both case covers and the other is bent, I will have to use this one, my 2 hour estimate was shy, I already have two hours in cleaning and still need to assemble it when the other gaskets come in).
I mentioned the moly oil for assembly. Originally I was using what I thought was the mixture aircraft mechanics use. I had misheard what my brother had told me. They use a 50-50 mix of STP and 50 weight, I had erroneously heard STP and 80 weight and had used far too a heavy oil thus far. Since it's not going to sit for 6 months before running it, I'm just going to use a mix of STP and the Honda HP4M moly I have (have a couple of cases) for the rest of the assembly oil. Between the moly and the STP, it should stay where it's put and provide ample lubrication for that first start up. Then I'll fill with bulk 30 weight I have, and change it shortly after letting it run a bit.
Other updates: the rear rims are at least half done in clean up. My son did that today after we laid them on the floor, it's a job to move those 26 rims with filled tires, used the hoist to put them down to work on them. They will get some POR-15 in spots around the stem, then AC silver, then clear coat this weekend. The clear coat is very difficult over the silver as it wants to pull it up (crinkle). I was able to do the fronts by very thin coats after thorough setup of the silver coat. I do think I even had a crinkle on the second time I did the fronts, but it was so slight, even with magnifiers, it didn't look it, just a hazy look under the shine. I went with it because it's a nice effect, looks like shiny galvanized finish. Whether it will last, only time will tell. Will be interesting to see how it works on these. I'll use acetone cutting again for a very quick set up since the shine is irrelevant, and that might let me get the clear coating done this weekend.
I really want to fire this engine up on the floor. I'm brainstorming how I can build a jig to hold it with what I have. It turns out I gave away the bell housing I had for the stationary version. That would have been so handy, and I'm kicking myself. Have this horrible habit of giving things away that people see and want when they visit.
Update: First rim is very close to clean enough to prime. I forgot how hard it is to clean up one of these without sand blasting. It's just down to the primer in spots and it was two nights effort. The second rim is mostly done but has a rusty valve stem hole. I really don't want to drain and dismount this rim, but it may be necessary. I'm going to check how much it would cost tomorrow. If too much, I will live with it and put POR-15 on it, then a washer over the open area.
Update: Both rims are primered now. The POR-15 was good as I expected, except in a couple of places. It flaked with absolutely no adhesion and I have no idea why. The stuff is hard as a rock when it works, but it's worse than useless when it doesn't. I didn't go over the rims with alcohol prior to putting it on, so I'm presuming there was something nasty in those spots that wouldn't let it bond well. That's a chance you take if you don't use their etch. I didn't bother to have the rims dismounted. In looking at them, I'll be replacing them in 3 years anyway and they will look beautiful, but with beauty that is skin deep. I have relatively new matched tires that I'm not putting on this time anyway. That will be a project for down the road. Tomorrow I'll get the Aluminum coats on, then let them dry for several days before clear coating, just to see if I can avoid the crinkle. I also managed to prime my 3-point draw bar today. Sadly, the last thing I needed to prime and forgot, was the leveling jacks for the 3-point. Noticed them tonight as I was closing up the shop. They aren't really a part of the tractor (totally non-original) so it's hard to remember them.
A humorous point about the masking in that photo. The paper I used was from a 1997 Yesterdays Tractors parts catalog. I had boxes sitting around the shop because a paper catalog goes out of date the minute it's printed, and we had to abandon that as a bad idea. It was a trip down memory lane to rip off the pages and tape them on. The world has changed so much now, there are no piles of newsprint laying around to mask things with. The old catalog sufficed. A useful tip is don't bother, just keep using blue tape moving outward on the tire as it is so much faster than trying to save tape and use paper. That's how I did the second one, and it was a half hour savings in time. Also, don't forget to go over the tire with cleaner (I used denatured alcohol) as the tape will not stick to the rubber if it's dirty.
Note the photo of the palnuts. I had trouble finding palnuts I was comfortable with from the normal fasteners vendors. At the airport, my brother showed me what he uses on an aircraft engine rebuild and lo and behold, they were the right stuff, and all tested to specs that make you comfortable putting them on a rod bolt. I looked up the site they purchase from (AircraftSpruce.com) and they were even reasonably priced. It turns out that if you don't purchase the aircraft fasteners with the government required certification proof, they lower the price to regular priced parts. Then they can't be put on an aircraft engine, but for a tractor that's fine, but all the fasteners they sell are tested to rigorous standards in order to have the certification. And they aren't the cheap ones people sell, which look like they are for holding furniture together. The reason I was so concerned about these, was what I found on ebay and even reputable fasteners dealers, looked like those things you find holding a recliner together. I could see these things floating around in the oil being turned into chards to clog oil passages, and felt quite avoidant about using junk from unknown sources. I had to purchase enough for the D15 and D17 to justify the shipping. The difference is that these have to withstand torquing to 60 foot pounds. Pretty easy to pretzel them if they are cheap.
Update: The Aluminum came out beautifully on one rim and nearly so on the other. Difficulty shown in the photo of the blue taped rim is where tiny flecks of that POR-15 appeared again. I didn't notice them when I was primering because of the lack of shine. Fortunately, the rusty areas I used it for, had no problem sticking. I'll have to sand those spots and hit them again before clear coat. The way this paint flows and the variations you get with aluminum paint, should make it pretty easy to patch. The aluminum paint went on nicely though, completely uncut because it's already thin. The 3M gun never ceases to amaze me. I'm getting several sessions off each paint head and they are about 5 bucks. The best thing is it takes me less than a minute to clean the nozzle.
Update: Sanded the POR-15 failure areas and recoated. Matched perfectly and I'm sure will look great with clear coat. One problem is that there a lot of brush marks from the POR-15. With this tractor, they will not be seen since the segment weights and final drives block all view of the middle sections of the rear rims unless they are spun out to full width, even then, it's well covered. That's hiding the imperfections, but I have so many tractors to do and only so much lifetime.
Update: Easter Sunday. Pictures didn't take but I got my first coats of clear coat on the rims, and a few other parts just to test the various colors (both of the D14 and Kim's D10). I also did a decal test using the same types I have for the D14. The decals were fine with the clear, though I was surprised that they are so thick, I don't think it's going to eliminate the lines around the edges unless I do a very thick clear coat. As expected, the POR-15 sections look pretty bad but won't show mounted. It was too cold (about 50 in the shop), especially since the clear manufacturers instructions say not to thin. I didn't because I didn't want to take a chance on crinkling. Surprisingly, I had none (except one small spot well hidden, no idea why). I went slow and put a dust coat on first, then blobbed on a couple of more coats after waiting. The blobiness was impossible to avoid, I used a 1.3 mm tip, couldn't get much out in a fan at all, so went to a 1.5 (I think) and that wouldn't atomize. I went back to a new 1.3 and it was better, but still not perfect. If I try a few more coats tomorrow, I will play with raising the air pressure to accommodate the cold and thickness of the paint (did this on a cub I restored in the dead of winter, required a lot of rubbing out, but it worked fine). Even coming out blobby, I was really pleased with how it self leveled. After the first real coat, I came back to expect orange peeled mess, and it was nice and shiny, yet not runny. I also did a test on the Rustoleum black I'm doing Kim's D10 Lights in, and that came out well other than the thickness I'm fighting. The last test was on the TISCO (Van Sickle) Persian 1 I've been using on the Tractor. I did one of my hitch components (for the 82R mower) and it came out perfectly. It does concern me that if I can't thin this, it's going to be very hard to get a smooth gloss on the sheet metal. It's not going to warm up much yet, and this guy has to be moved out of the shop when the engine is done meaning I have to paint the main part of the tractor soon.
4/2/18 Dropped below 50 today so the clear coating tests were out. I've decided to start clear coating the loose parts, starting with the back of the weights so I can test out some different pressures with this rather thick coating. We pulled off the masking from the rims and they look just fine. They don't have the gloss of some show tractors I've seen, but they are still quite a bit more glossy than I'm sure the originals were. Clear coat over Aluminum paint is beautiful. Will be interesting to see how it holds up on a working tractor. Tomorrow the temps should be back over 50 so hopefully I'll get a lot of painting done. I'm planning a jig to hold the front frame plates and wishbone solidly together to make this and the D15 and D17 easy to pull the front end off. I really dislike disassembling it when I pull the engine. Still have to fabricate the battery hold down and belt pulley shift linkage and have been laying those out.
4/3/18 I hit the finals with base coat since I will need to clear coat them and get the rear wheels back on. Ran out of paint from my gallon of Persian 1, I still have a quart but I don't think I'll get everything for this one done, may need another quart. I also used up the clear coat I had in the cup before changing the gun over to base. I brought the pressure up to about 32 and the un-reduced clear flowed out beautifully. I was doing the back side of the wheel weights to do this because it was kind a test. It went on a little thick, but I was able to do two coats before the cup ran out. I'm sold on clear coat. I used to criticize privately, that it was unoriginal, I was wrong. This is a great way to paint a tractor. It's beautiful and it should be more protective. I will say that the clear coat seems to darken it up though not as much as Persian 2. | | |
|
| 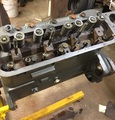 19:10 04/04/18
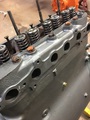 19:10 04/04/18
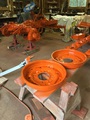 18:23 04/05/18
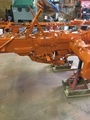 18:23 04/05/18
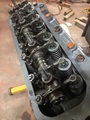 20:54 04/06/18
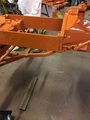 20:08 04/07/18
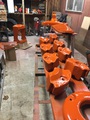 20:08 04/07/18
| 19:10 04/04/18 Head OnDuring the tractor time today, we put the head on. Torqued to 80 Ft Lbs just so I'd have some room, will need to torque again after running anyway. We had 2 1/2 hours to work and got all the pieces ready for clear coat, organized into one of the smaller bays of the shop so we can still do the base coat completion. In sanding down some of them, I burned through and that will mean a few will be re-base-coated. For the cylinder head process, we discovered that the studs had not been cleaned, so my son spent the majority of the time chasing down all the threads on those. Should get the rockers, oil tube, maybe the tappets adjusted, valve cover and water pump on. I'm expect my replacement front seal tomorrow so the front cover can go back on too if it arrives. The way I figure, after the pan is on, I'm going to leave the rest off and put the oil pump and flywheel on. I picked up a couple of 6 foot slings that should let me slip it in a bit easier without having to bolt chains to it. Otherwise, I would have waited and mounted the engine prior to putting the head on so I could bolt a chain to the head mounting bolt holes. But I used to build the engine completely and use a sling in the past, would rather do it that way. I decided to forego trying to build a jig to run it on the floor. Takes too much time.
I braved the humidity and painted the main part of the tractor, and what was necessary to put the wheels on. It will take one more session and I was shocked by the amount of paint I used. Fortunately I have another gallon on order. I sanded the hoods (2000 grit just to be cautious about more burn-throughs) today and started to worry a bit about the colors I'm going to have. They may mismatch under the clear since I base coated the sheet metal late last year, sanding it, lightens it up. I'll need to do some tests. But all these will be cleared as soon as the second coat is done. Then I may find myself recoating all the rest of the parts. I don't want to do that if I can avoid it. We'll still try to get the rockers on tonight if the shop clears out enough to be less toxic.
04/06/18 Got the rocker shaft on after a couple of tries. Keeping those push rods in the lifters was a little challenging since I didn't notice one was not in until after I tightened down the bolts. We used red thread lock on the studs to head but none on the nuts. I went over the valve opening sequence with my son to explain how this engine works, but we are leaving them loose until we can adjust them warm. The motorcycles I did as a kit, always gave a cold spec. That was a double edged sword because you had to leave the bike sit for many hours before adjusting valve lash. Painted the rest of the major parts today, then remembered that I didn't do the swinging drawbar. Haven't used it in so many years since the 3-point has been on this tractor almost continuously since it was new (to me, late 80s or early 90s). Will hit it when I hit the engine. Our plan now is to assemble most of the linkage for brakes, for clutch, and the floorboards, then clear coat the tractor itself and the numerous parts I have base coated and sitting in the other bay. Need to get the decals I'm going to use on too. I'm probably only using the hood, side sheets and PTO decals. The rest are kind of busy for my taste, and it's not going to any shows. Since the clear-coat-over-decal test was successful (my IB hood sports a Farmall Super C decal at the moment ;-)), I want any I'm going to use to be on before the clear coat starts. As I looked through the pack, I couldn't visualize having the others on the machine. Might change my mind, but need to do it fast if it's going to happen. It's a working tractor.
04/07/18 Hadn't the time to do anything but clear coating today. I didn't do the main frame but did do the finals and a test. The photo of the front side supports shows where I clear coated those but didn't clear coat the torque tube. I wanted to compare, and I was fortunately wrong, notice the color is a perfect match between the two, the clear coat didn't darken it all. The other part of that, is that this side panel wasn't re-based coated, but is from the painting I did last August or so. The torque tube was from yesterday, so all the way around, the colors are going to match. The other photo is of the weights and some sheet metal which had just been clear coated. Unfortunately, the door in that bay doesn't seal well and we were in the middle of a windstorm, dust in there blew on to some of it, lint really. Those will need sanding and buffing if I want them to look good. But boy to do they shine right now. Need to set painting aside and do some engine work and some assembly tomorrow. | | |
|
| 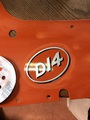 21:07 04/08/18
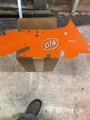 21:07 04/08/18
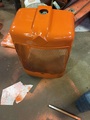 21:10 04/08/18
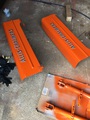 20:17 04/09/18
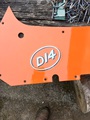 20:17 04/09/18
| 21:07 04/08/18 How not to do decalsI wanted the challenge of using mylar strip decals rather than springing for the individuals (they are a lot more expensive and thinner, much easier to do a good job with). I started with surfaces that were painted last summer with my old gun, very bumpy since it was just tossing blobs by the time I retired it. I sanded it smooth underneath where the decals were to go then cut the decals to the smallest size I could work with to get rid of all the excess mylar. Then I put them on and sanded around the edges to try to blend. The problem with these strips is that you have all this excess clear decal section that is going to look wrong when compared to the surrounding base coat. But I wanted to see how I could do with them. After sanding it, I went over and over pressing them into the still slightly uneven paint surface then concentrated on just sanding the entire panel smooth (not an easy job with how bumpy it was). It had two or three coats of very dry (and too thick) base coat, so it wasn't hard at all with 400 grit, no chance of burn through. Then I took them to the shop and put on a couple of coats of clear. They look alright, but all that clear mylar is still very noticeable.
I would have saved a lot of time going with the individual cut decals, because I know from guitar finishing, it's going to take me a long time to build up enough clear, then sand most of it off, to get the decal lines to be gone. Color-wise it looks pretty nice though, and I was sweating that. Unfortunately, I'm still running high pressure (32 PSI) with the unthinned clear coat and I did get some runs. They snuck up on me. The runs worry me a lot more, since it's going to take some serious drying time before I can repair them, and then I'll still have to shoot them again with clear, I will be on to some other restorations by the time these parts will be ready for actual finish work, can't sand them as much as they'll need until they have thoroughly cured, but this machine won't need the hoods and side panels on it to actually use it. I really need to resolve what the appropriate thinner is for this "acrylic lacquer" clear coat. I might call the manufacturer tomorrow. I don't care about the warranty or finish failure, I want it to spray well, I just don't have good control with it unthinned. I also put a shot in for the radiator shroud, it's looking very good (aside from the dust particles, wish I could afford a paint booth). I'll break it down with 1500, 2000 and should be able to get a mirror finish on it with rubbing compound. Getting runs, dust, bugs etc isn't worth losing sleep over, but for each flaw, I'll end up investing a lot of time getting the final finish the way it should be.
One thing I thought of today as I was doing the decals. I'm too bondo averse. I should have done some of the surfaces with filler. It would have really improved the final product. I moved decals slightly to avoid spots that should have been filled (you'll notice the D14 logo is slightly too far back if you are familiar with where they were placed).
My son spent the time getting the rear lugs cleaned up so they would go in by hand. They are looking good. He also started assembling the operator platforms. Want that done before the rear wheels get mounted. Today was probably the most time we have spent on this tractor this year in one sitting, about 4 hours.
Update 04/09/18: I shot a couple of photos, the first, the hoods, are more flattering than they really look. When you put them in the sun, the mylar squares are quite noticeable. I shot the side sheet after the clear had shrunk back and it's more realistic of how they look. It will take a lot of clear to blend them without lines. I need a lot of clear though to level the lumpiness you can see in the side sheet photo. I'm feeling confident that they will look very good after I do the work necessary. Individually cut decals would have saved me time, but many of the same processes would still be necessary to give them a seamless appearance, just less time and clear coat to do it. So, in the long run, the extra money for those would be justified. Given how long paint takes to really cure fully, I might see the lines start popping back out in a few months. We'll see.
Update 04/12/18: I've resigned myself to the fact that I'm not going to make the mylar strip lines go away. They are too thick. After some coats, they still seem as prominent as ever. I will attempt some light sanding at the edges and see how far I have to go, but I don't see them disappearing in any reasonable amount of clear coat. I don't want the clear coat to get too thick.
Update 04/13/18: Jury is still out on the mylar line blend. I sanded tonight after cleaning up all the bug holes in the clear and sanded around the edges of the decals a bit. There isn't that far to go. I may be able to get it so the decal is raise a little, maybe not noticeably, but without the lines. One serious mistake I made which you can see in the right light. I sanded the paint behind the decals and the color is off, in the right (or wrong) light. DO NOT SAND UNDER THE DECALS!!!! Put a fresh base on after sanding but prior to putting the decals on. I have trouble comprehending that I could be so dumb. I've never done it before. | | |
|
| 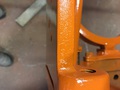 20:14 04/13/18
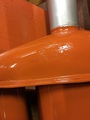 20:14 04/13/18
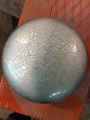 21:02 04/19/18
| 10:01 04/09/18 Tractor PaintI'm using what you would call "Tractor Paint" or Tisco/Van Sickle Alkyds. It's a very forgiving paint and made to stand up to the harsh environment that a work tractor lives in in most cases. There are tricks to using it which if followed, will create a very tough finish that will fade little and look great. It used to be with older tractor paint, you either got your brush out and painted or you thinned it and shot, then lived with the results. It faded, was often a wrong color, and was best brushed which didn't look as good. With the advent of clear coat, it's upped the game in quality, but also needs special care to make sure it will come out right.
Alkyd paint is a "plastic" sort of paint rather than an oil-based paint, that's how it creates such a tough shell that can survive on a farm implement. You could think of it in the same way as a wood finisher thinks of polyurethane, and the same arguments exist as to lacquers versus polys. It will tend to go on thicker in fewer coats, leaves few marks when brushed with a sponge painter, dries a bit slower, and can be thinned for spraying with a lot of off the shelf products. While the colors used to vary from OEM paints (back in the 90s when I was restoring before), this current generation of products is quite good.
The base coats need no special note other than you thin the solid colors well if you want to spray, and don't thin metallics much if any, since they will shoot from your gun without undue pressure. They go on well and if you get minor runs, they self-level fairly well. Drying time is important because when you get a thicker coat, it takes a lot of time for curing. Where you might shoot car paint twice in one day, the color coats need much more time than that with tractor paint. While these types of paints cross-link, that isn't important for good adhesion (though could be desirable) so drying it helps to avoid finish problems when two coats interact.
Where the drying time becomes critical, is with clear coats. On car paints, it's actually necessary to lay down clear within 24 hours or you have separation later. If you follow "how to clear coat" directions on the net, chances are you'll have serious problems. With tractor paints, the clear is too hot for the base to move that quickly, and really needs the cure time. It will eat down into the base coat, and pull it up into wrinkles completely destroying the paint job. Further, tractor paint clear coat states it should not be thinned. The reason for this is that the customers try moving too fast, not allowing drying time, and if it's thinned, it will require the base coat be very dry. You could visualize it that the hot clear is going to eat into the base somewhat, but it will eat further if the base is not dry, all the way down to the primer. Then you have the base coat "floating" in the clear unable to release it's solvents, and bubbling itself up (I believe a paint expert would be horrified at my description here, but it was a good way for me to think about it). You can simulate what's happening by taking some lacquer thinner on a rag and rubbing a piece that was base coated a few days prior. You shouldn't be surprised when the rag comes back with color on it. If you do the same with a piece that was painted within 24 hours, you can probably take the paint right off even though it seemed dry. It takes a long time for paint to cure.
I inadvertently did this in an earlier blog with the front rims for this tractor and the D10. I shot them and the next morning, since they felt dry to the touch, I shot them with slightly thinned clear coat. Spots that weren't completely dry, wrinkled and had to be redone. I also did it accidentally this week, you'll see the photos to the side. I had a light base color spot on the top (I'd used brown primer on those and it was showing through) of the front side support beam so I'd touched it up with a sponge brush knowing that no brush marks would show in a rough steel piece like that. I also repaired a small spot on the air cleaner where a bug had landed (and I messed it up by trying to pull it out while the coat was wet). By shooting clear over those after about 24 hours, you can see the results. The clear completely lifted up the semi-dry base color and made a mess of it with wrinkling. Though the long-dried base that was already on there, was completely unaffected. Now I'm waiting for that mess to dry so I can re-sand, put base coat back on, then let it dry for 48 hours and try again. If I were to thin the clear, then I'd have to wait even longer (which I probably will), even up to 5 days just to be safe.
Normally, you get wrinkles and lifting with other paints because you are trying to paint one type of paint over another and they are incompatible. The wrinkling occurs for a similar reason but it's not incompatibility with this type of paint and clear. It's totally a matter of drying time before application of clear coat. Note: I've heard that long dry times will also help with normal wrinkling issues such as lacquer over enamel. In other wrinkling issue, it can be the over coat that wrinkles rather than the base.
Since the manufacturer officially does not support thinning of their clear, you are on your own to do so. If you're spraying, you either have to thin, or crank up your pressure to get it out of the gun and that's not optimum so I felt thinning was necessary. In my testing, lacquer thinner (which I normally keep around only to clean my gun) works, but makes the clear coat very hot (more color coat drying time needed before using it). I've not tried acetone and mineral spirits yet, but I expect mineral spirits will work (maybe even better) and it will make the clear the least "hot". Acetone, I only use to try and get a quick dry on the base coats when it's too cold to be painting, but I'm guessing it would be a mistake since it makes for a duller finish on the color coats, and that is the last thing you want on a clear application.
Update: Just added the air stack cap. It was a perfect example of the metallic paint being "dry" for 24 hours. I thought I would mist it with clear. It didn't work. By the time it was a gloss finish, it was crinkled up. Rework due to moving too fast. | | |
|
| 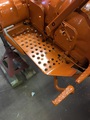 20:35 04/09/18
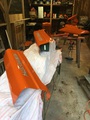 19:34 04/12/18
 19:34 04/12/18
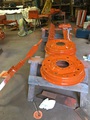 19:34 04/12/18
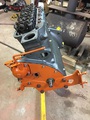 20:05 04/13/18
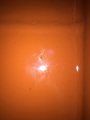 20:05 04/13/18
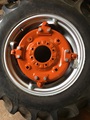 19:37 04/15/18
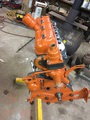 19:36 04/16/18
| 20:35 04/09/18 More AssemblyPut the operator platforms on and hooked up the brakes. I also started on the clutch linkage and a few other things. The only thing of note, was that in moving things around to paint, I lost track of how the parking brake goes on. It turns out the casting has it's flat side (of the tab that connects to the linkage) on the tractor side. From there it's easy. Just can't take enough pictures as you disassemble.
Update: Spent today's tractor time paint lugs and the eccentric nuts aluminum. I have studied every video and photo I could find of original D-Series ACs. They almost all have silver lugs and eccentric body nuts. On the forums, one person read off an account that said they did hand paint them initially and switched to cadmium plated nuts. From what I found today, it appears that all the way up through the Series III machines, the power adjust wheels had this arrangement, at least on the eccentric nuts. The lug bolts were a mix, sometimes cream/orange (depending on year) and sometimes silver. Definitely on the early machines like this 57, they are silver. Obviously it will take touching up after I install them. I also painted all the fasteners that I'd let slide and touched up Persian #1 on various parts I hadn't worried about. This will be the last base coating excepting the engine when it's done. I have photos but they are boring, just nuts and bolts. Surprisingly, this process took another 4 hours or so to get them painted.
Update: I shot a nearly everything in clear today. The sun came out and bugs were everywhere. I unfortunately ended up with about 12 in the finish of various parts. Disheartening (probably for them too). I'll have one more round of clear. I'll clean up the bug issues after it dries enough, the shoot it again. I'll get more bugs of course, but it's supposed to rain tomorrow, and possibly I can sneak by them. It's frustrating that if you paint in the dead of winter, the paint doesn't go on as well, but if you paint in spring and summer, you have so many bugs landing on the "cool bright orange thing" that it's hopeless. No mechanical work today due to doing three pots of clear. Still have a lot of wiring and the engine to finish, but now the bulk of the painting is starting to be completed. One more major session and all but the engine and a few fabbed pieces will be done.
Update: 04/13/18: I put an example of the bug damage. This one was the worst, I made the mistake of picking it out while it was wet. Bug guts all over embedded in the clear. This was the radiator shroud and was looking beautiful (I have to admit I'm a little upset about this, both hoods, one of the side panels, one of the wheel guards, and the shrouds all got hit by this, a bug can do tremendous damage where the clear coat has already cross-linked to the previous coat, two coats get destroyed, very upsetting). A lot of sanding needed but the clear coat has to cure first or I'll burn into the base coat immediately. So much engine work and assembly is needed that I'm going to take a rest from painting until I get ready to paint the engine. I have some other paint issues I'll add to the previous section. (Edit: sanding the bug guts out didn't expose the base coat, whew, while I was at it, I sanded out the collected dust particles in the finish of the sheet metal parts. I think the next coat of clear will be the last for all but decal bearers, those will get several thinned coats).
I also put the shot of the front cover. It's back on again. I am troubled by the front seal. It didn't feel like it seated well. It wanted to pop out repeatedly, and I noticed the spring at the rear, wanted to come loose. I'm hoping it's not floating at the back of the seal plate. If it pours oil out, it will mean the engine gets pulled again. Edit 4/14/18: Today I put another seal in the extra front plate I have, seated it as far as it could go and checked the difference in height. It looked to be somewhere between a 64the and 32nd. That troubles me a little, but I know the spring isn't behind it, could easily be the difference between the two plates and two different brand seals. I also put the pulley on and spun the engine over to get it to #4 TDC. I could not do it by hand except a little at a time, but putting a big wrench on, it turned rather easily and felt smooth. Nothing like the last time when the seal was tweaked. Valve lash is adjusted to .015 cold (thanks to DrAllis' post the other day, I was going to leave them really loose and adjust warm, if this works, what a great way to save effort).
Update 4/14/18: I put other comments above, but one new thing is that as I sanded out the air cleaner wrinkles (mentioned in the previous section), I took it down to bare spots. I am thinking it might be rusting from the inside out (it sat dry since mid-2000s so it wouldn't surprise me). If so, I have another, but it will require clean up and paint. I'll lose the air cleaner decal, but I'm questioning if they put any of the decals on besides the four main ones anyway on a 57 and if they did, it was probably the yellow B style, not the red one supplied. Will take my endo-cam up there tomorrow and look inside, the last thing I want to do is to suck rust into a fresh engine. If we put the time in tomorrow, we should get the pan on, the water pump, governor, distributor and get it on the floor so we can do the rear seal, flywheel, clutch and pressure plate. Then goes the oil pump, filter mount and all the tubes. I am excited about the next step since I'm trying a different clutch and pressure plate part number from a later G-149. Gotta get those rear wheels put back together and mounted in the next couple of days too.
Update 4/15/18: One rim put together. If anyone wonders how they go together, you place the tire flat, hold the rim up with a something that won't get in the way of your hand going in the hole, slide the eccentrics down the rails into place and put a bolt into hold it. Three more and your there. Also started buttoning up the top of the engine. Knocked off at the water pump. Before the valve cover goes on, remember the oiler tube from head to rocker tube.
Update 4/16/18: I decided to use gasket sealer, non-hardening #2, on the valve cover and thermostat housing, so pulled them and reassembled, plus the water pump. Also put the second rear wheel together (eccentrics) and got the release bearing and clutch linkage reinstalled. Turned quite cold again so couldn't finish up paint work, just as well because I certainly know better than to rush clear coating the touched up parts. Getting anxious to get this thing done and get on with the D10, plus I will need it very soon to bush hog. Of course, there is a good chance of a lot of rework with this new engine, wiring will surely take me longer than I plan, many small things to go wrong.
Update 4/17/18: With the top of the engine all buttoned up, we put the oil relief valve back in and mounted the crankshaft pulley. Spun it over and installed the palnuts on the rod bearing bolts. The manual specifies 40-60 ft lbs for the palnuts, but even with a 6 point socket, we could get no where near that torque on them. The start to deform long before that and you slip off them. We got them as tight as we could. I now recall that last time I used these, I used an open end and just got them as tight as they'd go. On the painting issues, I had a run in the air cleaner cap I hadn't noticed, it was in the clear coat, but when I tried to sand it out, I burned through to the primer. I sanded it all down back to primer but didn't want to mix the Tisco Aluminum paint for just one small part. Instead I took a sponge brush and painted it by hand. To my amazement, this left no brush marks and looks fantastic. I'll be clear coating it with some other parts in a couple of days, I have observed that 48 hours is not enough dry time for the clear coat formulated for Alkyds. I will give this part several days dry time before hitting it with clear. | | |
|
| 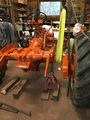 21:02 04/18/18
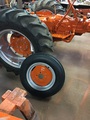 21:02 04/18/18
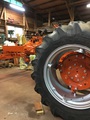 21:02 04/18/18
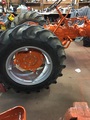 21:02 04/18/18
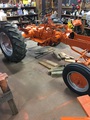 21:07 04/19/18
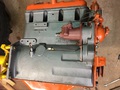 21:07 04/19/18
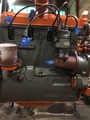 04:40 04/22/18
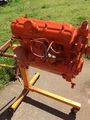 05:39 04/23/18
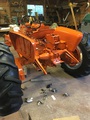 07:43 04/24/18
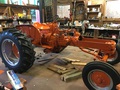 07:43 04/24/18
| 21:02 04/18/18 Rear tires onWe pulled it off the jacks today, exhilarating to have the rear wheels on. Not an easy job when they are filled. Also did more clear coat and surprise, the lines from the mylar decal strips actually disappeared this time. I sanded them once more before this coat, and it's getting very close to seamless. Sad that I sanded under the decals because you can, in the right light see them because they have a slightly lighter color. If you are going to try using mylar decals under the clear, just be sure to coat a good base coat that needs no sanding other than 1500 or 2000 grit, and then put the decals on. If I'd done that, you would not be able to tell that these are mylar strips. Can't believe I proceeded without realizing the potential issue, sometimes I'm just dense. I also wrinkled up my beautiful air box cap for the same reason. After saying above I was going to wait days, I thought I could beat the system and do several non-gloss coats, I gave it only 24 hours. It had come out so perfectly, but I didn't wait long enough to clear coat. I think 5 days is a minimum with metallic colors like the aluminum (this is only for alkyd based paints and clear). I'll be painting that darned cap yet another time. Maybe I'll wait till I do the D10 rear wheels so I don't crack open the paint too much (next time I open the aluminum, I need to separate into smaller air tight containers). Note the photo with the front wheel next to the rear. I used a store bought poof can clear like Rustoleum on the fronts. Looks terrible comparatively. Not only is it nearly satin, it's yellowed compared to the Tisco / Van Sickle clear coat. I will not do that again. Minor problems aside, it was a good tractor day.
Update 04/19/18: Front wheels on, distributor mounting housing on, oil pan on, tightened up all the bolts on the ops platform and hooked up the brake springs. Also mounted the hitching brackets on the PTO case just to get a bit more out of the way. I'll get the engine primered tomorrow so I can paint it. I can't hook up the oil pump and clutch until I can take it off the stand, and it would be much easier to paint it on the engine stand. Sure looks nice with brand new tires on the front. Figuring out the oil line routing was surprisingly confusing. Then I remembered I had two other G149s sitting in the barn, went over and took some closeups. It's not so complex as it seemed. I'll need to do a section on that in case someone gets an engine and rebuilds it which had no oil lines included.
Update 04/21/18: Got the engine ready to paint by putting old plugs, cap, oil filter, and wires on it. After I shoot it, I'll disassemble it partly so it can be mounted, but also so I don't paint these parts. It's not very accurate to not paint them. But I can't see painting replaceable parts. I will do a section on installation of the distributor and timing but I think I'll do that as an article rather than a blog. I already have one on magneto timing for ACs and Farmalls, and this would be a good companion. I'm wondering now about clear coating the engine. Since this is my first clear coat job, I really don't know. The question is how well the clear would hold up on an engine. Will research while I'm waiting for primer and base coats to dry.
Update 04/22/18: I painted engine and everything else that didn't get painted, small parts mostly, carb, intake manifold, various oil hoses, miscellaneous bolts, and the rear bullet lights (in black) since they came in chrome. So minimum clear coating day will be Thursday (allowing dry time of 96 hours prior to clear). Painting was a joy for the first time this year. A nice warm sun and lower humidity made things set quickly. Pros use a different gun for primer from base or clear and I really see why. Once again, I used the same tip to shoot primer and base, and found that some flakes of primer had dried in the tip, then came out during the flow of the base coat. Nothing serious, but from now own, I'll use separate primer and base coat tips. This happened to me last year too with my old gun. With the 3m system, there is no excuse, you have extra tips and the two do not need to be mixed.
There is little left to do now without putting the engine in, and that will need to await clear coat and dry time. While I wait for that, dash wiring and associated assembly can occur. Fenders, toolbox, dash, seat, gauges, wire, tank, battery box, and fabbing box lid and pulley actuator arm. Mon-Wed nights should be fun doing all that. Clear coat on Thursday and perhaps clutch, oil pump, and engine mounting on Sunday. Then it's final wiring, timing, tuning, oiling and testing to see if I did something horribly wrong inside the engine. It would really be nice at this point to get this done and roll the D10 in the shop. It's a much faster restoration. Probably still a couple of weeks left on this one at the rate I do things, plus with the weather change, need to take time for planting and garden fencing.
Update 04/23/18: Assembled Wheel Guards, toolbox and seat. Since the wheel guards had set for some time now, I did some sanding with 1500 on some orange peel areas, then auto polishing compound, and finished with Guitar polish. It looked great for a working tractor. It knocked down the brash gloss of the clear coat and started to look more like a showroom finish on a factory tractor. A lot of work to do that by hand, but I have never been happy with my buffer, it just doesn't do the job that hand rubbing seems to do. I don't know what sort of rotary unit pros use but I will look into it. When you start rubbing out the finish, the lack of using bondo really shows. Old dents and rust pits do impact the finished look. Still looks very nice for a working machine. The proof will be how clear coat stands up to scratching from weeds and brush. It does seem to be nicely hardening up though. Next step really should be the re-wiring because there isn't much else to do waiting for the engine paint to dry enough for clear coat. I might rub out the instrument panel first since that would be tough to do with the gauges mounted.
Update 04/25/18: Definitely having problems with the paint. I guess the cold and not thinning the clear is coming back to bite me. The clear was way too wavy and is taking a tremendous amount of sanding (1500, then 2000), and even then, it will not level out to be anywhere near a show quality job in some spots. The fenders are coming out nicely, but the side panels, which I shot flat (and thus thick) are the biggest problem so far. Spent at least 3 hours on one panel and couldn't get it to where I liked it. Sure will be a pretty working machine though. The shot of the side panel with some weed flowers was my attempt to show how much the mylar decals flattened into the clear. Better than I thought it would be, but worse than what I wanted. | | |
|
| 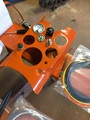 20:51 04/25/18
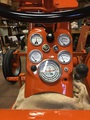 21:33 04/26/18
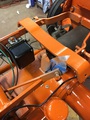 21:46 04/26/18
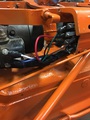 21:14 04/27/18
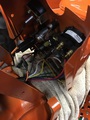 21:14 04/27/18
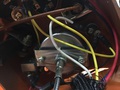 20:59 04/28/18
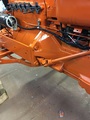 07:16 05/08/18
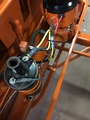 07:16 05/08/18
| 20:51 04/25/18 WiringI started on the wiring today, which actually meant just getting the dash ready. With all the new paint, getting the dash light to have a ground was surprisingly hard. Took a lot of grinding and clean up. The light switch will be the same. The other controls either need no ground or have an external wire fitting which will supply ground. It took me about 2 hours just to take the dash this far, so no actual wiring, just prep. Excuse the dash paint, the old pitting really showed through without bondo.
04/26/18: Did about a quarter of the wiring, had to put gauges in and spend quite a bit of time grinding paint for good grounds. Should finish it tomorrow unless I run out of wire. I underestimated on the runs to the front and back lights. Aside from that, the estimates were good. I'm considering not hooking up the lighter. I can't see why I would want a lighter functional on a tractor, and it's a direct unfused feed from the Ammeter. It seems a potential place for fires and I'd never smoke when in a field anyway, nor do I need to charge a phone on a tractor. It bothers me a bit to have an non-functional piece there just for looks, but I may leave it unwired. One thing, it was great to put in an original style Voltage Regulator. I had an old car one in there that was much longer and it made the space far too tight, the starter would usually take me 15 minutes to just rotate it to the right position where it could back out. Now it's expansive in that area. BTW, every step of the way, I kept the VOM handy and tested the grounds to make sure every part involved and the main frame all had good clear grounds.
04/27/18: Finalized all wiring that I can do prior to the engine going in other than the tail lights. It's taking awhile to do those. Snaking the wires through the wheel guards is a chore. I got one done, but it took about 45 minutes just to move one wire 2 feet. Got the main loom on and am slowly working a smaller loom to the rear for the tail lights. It's very nice split loom and has a traditional look. If I were doing an accurate restoration, it should be painted along with the tractor, but the black offsets the orange very nicely.
04/28/18: Taillights are on and done. Everything is wired up but the front end (waiting for the engine) and the battery cables. I'm trying to figure out if I need some changes on the solenoid before I finish the battery cables. The conflict with the choke rod makes me think something is wrong, which may mean I need a different solenoid. Tomorrow is painting for parts I missed. Front light shells have no clear on them, plus I've discovered so many touch up spots in wiring this up (and created more than a few in the process. I also discovered a conflict for the belt pulley actuator arm. It won't clear the light switch. I'm deciding whether to pull the pulley and put it on the D15 instead or keep it and get a new light switch. The switch is obviously from a car from long ago so it's the long type. It's in the lower left corner of the photo and you can see light from the hold for the pulley actuator. No clearance there.
05/01/18: The AC D14 didn't have a main fuse protection. I checked out the circuit breaker response times and they were not too fast unless you got a low amperage switch. Since I had purchased a spade style fuse just in case, I installed it on the main coming from the battery just downstream of the input solenoid connection. I'm putting a 30 amp fuse in it since it's a generator system and I'm guessing that it would take a short to trip it. I have a 60 amp ammeter in the dash and that should be good for 100 amps before it smokes, so this should handle any catastrophic failure, and I can go to a 50 amp if the 30 can't handle it. I still have the stock lighting circuit fuse wired in and will use a 20 amp there. I'm thinking that the most likely short condition usually would occur in the lights, since they are exposed to brush. This way, the light circuit can blow, but the tractor will still get back to the shop.
05/07/18: Wired up the coil, distributor, and ballast resistor yesterday. I'm putting a Pertronix Electronic Ignition in this one, so I'll finish that today. It's supposed to have a 3-ohm resistor inline which mine shows as close, but the instructions don't say if that's warm or cold. I've been told a ballast resistor changes dramatically on warming up. | | |
|
| 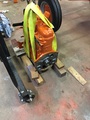 08:00 05/02/18
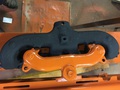 08:00 05/02/18
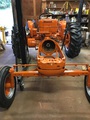 08:55 05/02/18
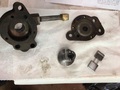 11:27 05/03/18
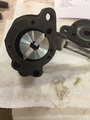 11:27 05/03/18
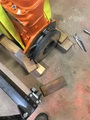 11:27 05/03/18
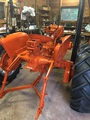 11:27 05/03/18
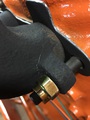 06:59 05/07/18
| 08:00 05/02/18 Engine BackFinally have the engine off the stand and am ready to rebuild oil pump, install and install rear seal, flywheel, clutch and pressure plate. The manual want's .002 end play or less from the oil pump, which suggests no gasket sealer can be used on the pump cover gasket. Kit comes with 4 gaskets. If the clearance is loose when it has the new rotor in, I'll need to lap the face of the pump body which should clean up any issues that might leak too (I hope). Not confident on this op since the cover surface is not as smooth as I'd like and I'm concerned I'll have a leak. Bevels on the Rotor blades are supposed to be installed toward the direction of rotation which since from the rear, the crank turns CCW, the cam must turn clockwise. Today I may try to get the back buttoned up and ready to mount.
The exhaust manifold should have been all orange, but I used 1700 degree flat black since the paint doesn't last and you get a lot of rust. The outlet to the muffler glows a dull red at night so I'll see if this will work. In the past, I've painted the entire manifold orange with eventual rust. May be no way to stop that, but I'll see how this works.
I was happy to note that the steering box/front support seals are holding. The most important seal is the main seal for the central steering gear and the part is not easily available, but I was able to match up a Timken replacement that is much thinner. I used two and it seems to be working. Of course it hasn't been driven yet so we'll see. My memory is not great, but this tractor may never have had oil in the front case since when I filled it during this restoration, it all dribbled out through the bottom seal. I used 8702 and 15005 SKF seals on the two seals for this case. We carry the input seal now, but I had to pick up the output seal from NAPA. Hopefully we'll start selling the output seal too since I know we can get it from Timken.
Tank and Battery box are on.
Hitch is on.
Oil pump rebuild kit comes with springs, rotors vanes and rotor replacement (plus gaskets, extra springs (don't know why), and a relief valve spring that works on the B/C/CA/IB). There are gaskets in the kit to fit both styles of pump, and you use only those for the pump you have. I found that I couldn't get the .002-.004 end play with my original pump and had to mix the cover from one of my pumps with the body of the other to get the right tolerance. It may be a little loose, but not much. I installed the pump and filled it with oil (which I'll repeat before buttoning up the engine to test). Rear seal and retainer and the flywheel are on. Will put the clutch on, centered as well as possible, lightly grease the pilot bushing and the engine will be ready to install.
05/07/18: The exhaust manifold crack on us when we were putting it on. I wasn't watching my son install it, but someone on the forums suggested it may not have been true. I'd trued it up several years ago and didn't recheck so it may have been warped. I'm not sure how setting on the bench for 12 years would have warped it but it's possible. My first attempt to fix will be TIG weld it with EZ-Weld wire. If that works, great, but I'm skeptical, or at least unconfident. I've never welded cast to speak of and especially not with TIG. The wire says 100 amps, 1/16th electrode and do small sections less than an inch. Since the crack is all the way through, I'll vee it deeply but still try to not open a gap. At 190 bucks for a manifold, it's worth a try. UPDATE: found a guy who will guarantee the weld, so I took the manifold to him. In the meantime, I'm going to try to separate a manifold and head I have that is in horrible shape. It can't accept a muffler, but I could at least do starting tests and timing while I'm awaiting the welding.
Note on Flywheel. While I was doing the flywheel, before mounting it, I went over it with alcohol and then naptha to get it really clean. I used LPS to stop the flywheel from rusting since it sat so long. That worked well, but it's really important to get it all off from the clutch mating surface. Naptha worked really well, I would have tried acetone too but forgot. It's just as important to make sure there is no oil or grease on that surface.
05/09/18: Radiator and front wiring are done. Will be mounting the shroud and running a test of the starter tomorrow. | | |
|
| 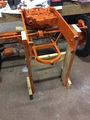 21:19 05/03/18
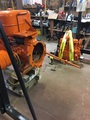 21:19 05/03/18
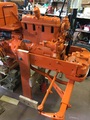 07:53 05/06/18
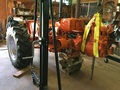 07:53 05/06/18
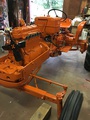 07:53 05/06/18
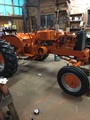 21:15 05/09/18
| 21:19 05/03/18 Engine MountingI was about to weld up an a-frame to pull the front end and decide the weight was just not that much, so I used 2x6s. It worked great, my son and I skidded/rolled it out with very little problem. It's extremely important to have the brace across the bottom or the lower wish bone just falls out of the front pin. I'll be making a different one for reinstallation, as it may not fit under the oil pan. Felt accomplished and saved myself several hours of fabrication. Now I don't know if it would be strong enough for the D17D and D15D, will cross that bridge when I come to it. I think tomorrow might be the day to mount the engine. Clutch is on and centered as best as I could with the wrong centering tool. Since I have the later pressure plate and clutch, it will be time to cross my fingers when we put it in and test if the clutch works. If not, the engine comes right back off. Also did some minor paint touch up and finished the extra parts I'd forgotten to paint. I still completely missed the swinging drawbar, I never use it so it's not been on in 30 years, but I noticed it again as I was leaving the shop and feeling guilty for ignoring it.
Update 05/04/18: The mounting didn't go well. I couldn't line the clutch up by eye well enough and then jammed the clutch splines till they couldn't slide on. Had to pull the engine back off and file the ends of the clutch hub splines. Now it slides on easily. One of the problems is that I am not balancing the engine correctly and don't have a balancer, just straps. I was thinking about fabricating a balancer, it would be so much easier to get the engine at the perfect angle. To rectify the original problem, I took the centering tool provided with the kit and found a bushing to increase the size of the tip from the pilot bearing (which is not used on the D14) ID to the pilot bushing ID (which is what the D14 uses. It was too late to continue by the time I finished that. I also spent time bringing the engine to TDC Piston #1 since I'll have to time the distributor once it's mounted. I got pictures of the way I do it using a balloon and pressure hose from my compression gauge and will write an article for the article archive. People constantly ask how to time their tractors and I have a magneto article, but never wrote one on a distributor ignition. I also made the markings on the flywheel obvious with light paint in the grooves wiping off the part not in the grooves. I picked up my filter, electronic ignition, plugs and wires at the warehouse today so those will be going in once the engine slides home.
Update 5/5/18: This time the mounting went perfectly. The alignment tool worked. I lined up the clutch shaft splines to have a slot at the absolute center and the clutch splines to have a tooth in the center. We raised up the engine as level as we could to match the angle of the tractor. When we backed it in, it was still balking, but my son suggested we put long bolts in and pull it on. I was resistant because I could see that jamming the splines, but for a fact, it worked instantly. Went right on. Bolted it up and slid the front end up to it, at that point realizing that the side plates would not clear the front engine mounting plate. To get it on the rest of the way, we removed the front mount plate and slid it in, putting the mounting plate onto the side plates. This was not the way to do it, but it worked. The jig to keep the front end together, should splay out to really work. I'll design something like that for the D15 and D17 and make it out of steel. First thing I did was check to see that the clutch was functional, and it appears to be even if badly out of adjustment. That was a fear since I'm using the clutch and plate from the later style D10/D12/D15.
A stupid mistake I made was one of the lifting straps, both of which are the continuous type, was on as a loop rather than a sling. I thought I double checked that when I wrapped it around the engine, but I had to cut one off. It's a shame but with plates bolts and hooks, I'll turn it into a choker for logging, we needed a new one since my old one broke and the diminished lift capacity will still be better than ropes. The mistake really started when I bought them. I wanted looped end straps but somehow ended up with continuous. They are rated way beyond anything I'd ever pick up (12300 lbs) and I didn't need them. | | |
|
| 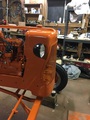 21:51 05/14/18
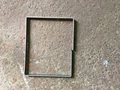 21:51 05/14/18
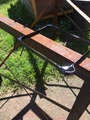 21:51 05/14/18
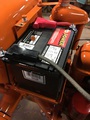 21:51 05/14/18
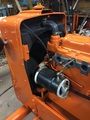 21:51 05/14/18
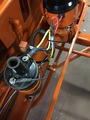 21:51 05/14/18
| 21:51 05/14/18 More Wiring, More AssemblyMade the battery hold down and hooked up the battery, tested all the circuits, every thing worked great except the dash lamp which wasn't getting a good ground. Nothing else needs a ground on the dash but the lamp and the lighter. I hooked a separate ground from tach to the lighter which gave a good ground to the entire dash. The tach is rubber mounted, but the the tach cable makes it a good ground. Battery hold down was designed after the original, but with a smaller profile to match the smaller battery I'm using. I messed up on the tie strap loops and ended up with the washers on angle. I will have to weld a half washer to a full washer to accommodate that. It came out okay though for what was a hunk of 1/2 by 1/8th bar stock.
I clear coated the lights because the black was too dull, then finished all the front end wiring and after popping and replacing the 6 volt bulbs that I forgot came with the lights, they work great too. Everything required figuring out and cleaning up the ground path, but grounds are good all over now.
I started working on the gas line. Contrary to what a lot of people say, I'm using both a sediment bowl and a separate filter. There is too much into this engine to allow anything to get into the intake tract. I made one serious mistake and didn't photograph how the two springs were connected on the carb to governor connection. It's not like the D10 or D12 nor do any of the manuals give a reasonable clue.
Did the starter test today and it works great, not at all laboring.
I'm also working on the temporary manifold but as usual, I'm instead of treating temporary, trying to restore it, get the muffler mounting bolts un-seized and removed. I doubt I'll be successful with that but it will feel good to have a spare anyway if I am. I have 5 G-149 including the two blocks and I'd like to have as many spare parts as possible.
Spent an hour and a half cleaning up the front badge. I didn't want to scrape the paint out of the background, so I put it in the ultrasonic at 50C in pinesol. Once again, the heat and pinesol melted the paint out and I was able to pick the rest out. It also shined the chrome up and it looks beautiful. Now I have to figure out how to paint it. I think I'm going to use a very thin mixture and a syringe to drop it in. I have so many left over from vet visits, it should work well and be controllable.
I don't know if I mentioned it, but I put in the Electronic Ignition. The shot of the coil shows the wiring is different from the stock distributor leads. It was shockingly easy to install. I took my best shot with the timing of the distributor, may require pulling it out again. Magnetos are so much easier to time.
BTW, the lights are the wrong type I know. The way I order parts is I just mention what I need to the sales manager and he puts it on a stock order (the slow boat). I just assumed I'd get the pointed back lights, but unfortunately, I got the round backs like should be on the WDs. It's a working tractor, it's not going in any shows, so... the sad part is I have a pair of stalk mounted WD lights that I could have used had I known I'd get these. Next time I have to remember specify part numbers. I'll also have to get me a WD one of these days to use those original lights ;-). | | |
|
| 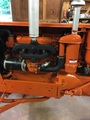 09:28 05/18/18
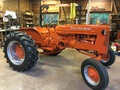 09:28 05/18/18
| 09:28 05/18/18 Fluids and timingThis is getting down to the home stretch. Since I broke the manifold and am waiting for the welding to fix it, I mounted the one my son cleaned up. We are not totally comfortable trying to start the tractor with it on there, because I could only Dremel the intake portion of the manifold so much, and if there are any chunks of scale down where I can't see, it could come loose and destroy a valve. Frankly, it looked extremely clean in the intake portion so it's unlikely there were any loose spots in there, but I'm mulling it over. If I decide to risk it, I can fill the antifreeze and start timing the engine today. Once it's running well, it's basically done until the original manifold comes back. I can't use this manifold permanently because the muffler mount bolts are frozen in it and have defied my attempts at extraction.
The only parts not on yet are the left side panel and that manifold. I also need to sand and buff out the paint, too many spots are orange peeled. That is a massive exercise to hand rub, but where I've done it, the paint looks beautiful. | | |
|
| 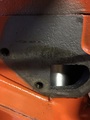 08:26 05/20/18
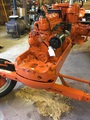 20:45 05/18/18
| 20:45 05/18/18 A new lesson...... in watching what I'm doing. After having all of the tractor together, my worst fears were realized, only in different manner than I'd thought. I filled the antifreeze and every bolt opened up and poured it out. The manifold studs and the water pump mounting bolts. Well, we were quite good at tearing it back down, draining the radiator and getting it ready to remedy the situation tomorrow. All these fasteners should have had thread sealer given the block was freshly cleaned, but I plain forgot. I used thread sealer on the head bolts because it was so obvious to me, but I neglected all the water jacket through bolts otherwise. Tomorrow it will go back together again. Looks pretty sad tonight though.
In the second photo, lower center, note the casting seam protruding. It was this which caught the body of the water pump and held it out. The bolt holes were seeping, but this was the major leak. The water pump backing plate was floating as a result and the large leak was between the backing plate and the pump cast body. I'll grind this down for starters, but now I need to disassemble the water pump and make a gasket for the backing plate. Either that or buy a new pump. When I wrote the above paragraph, I hadn't removed the pump yet and couldn't see where this had created a conflict to the fit. My original block did not have that protrusion.
Update 05/20/18: I removed the burr on the casting and put it all back together correctly. One drip remained when I filled the coolant. I don't think I'll be able to correct it without a new water pump. I was unable to get the screws broken loose that hold the backing plate on, and it is seeping slightly from there. I am trying to decide if I want to get a new pump or chisel this one apart and seal it up. I'm also going to check out the other D14 water pump I have, see if it would be easier to pull apart and seal up. The good news.... I have spark. I had an issue with the new key switch I bought where for some reason, I had to use the accessories lug to run the ignition when the key is in the On position. I thought I'd tested that thoroughly but it wasn't working. When I moved the output to the other lug, the spark came through clear and strong. The bad news is I have a cross-threaded bolt on the carb. I don't know how I did it, and haven't done that since I was about 13 and cross threaded the spark plug on a 10 dollar Honda C110 I picked up. So the carb is going to have to come back off yet again to check it out. It doesn't feel right as if it's about to strip and it looks crooked to me. If I find I cross threaded it, I'm going to feel pretty dumb. I cleaned up my other TSX tonight just in case. It's going to be in the ultrasonic for a couple of days. It's looking like it will clean up well though. Before any of that, even the water pump, I'm probably going to start it first just to see if I have the timing right and no fuel leaks. It is a bit demoralizing to have the coolant leaks, the header swap thats coming, and the issue with the carb. I'd hoped to be done and bush hogging by tomorrow.
Update 5/22/18: picked up a new water pump from the warehouse and let the coolant drain overnight, installation today. We also did a fuel line test to see how that all was going to work and to try and start it to check timing. It was shocking how much scale came out of the tank and the sediment bowl was restricted by gunk I must have missed. I just put a new on on. I was letting the sealer dry overnight and we'll do a another test of that today. I have to mention that leaving the tank cleaned but empty for several months was a large mistake, I had run alcohol through it, then sealed it, but that was clearly not enough to stop rusting. I'm hoping the tank isn't damaged to the point of needing sealing. We will find out today. | | |
|
| 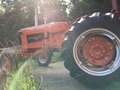 07:25 05/26/18
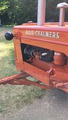 07:25 05/26/18
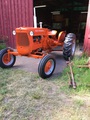 07:25 05/26/18
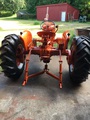 07:25 05/26/18
| 07:25 05/26/18 Finally DoneFinally got the water pump sealed (by buying a new one, the old one felt like the bushings were rough anyway) and reassembled. We started with the old sediment bowl, but finally replaced that too. The thick varnish scum inside was not even dented by cleaning it. I'll save it and reuse after I put it in the ultrasonic. After it was all together, we gassed it up again, then tried firing it up. It ran immediately though sounded like it was only hitting on 1 or 2 cylinders. I retarded the timing until it started purring and locked down the distributor, will need to put it on a timing light but couldn't find my old springs that go between plug wire and plug (haven't used the timing light in too many years I guess). The only thing that concerned me was it required just a hair of choke to run right. Might be timing but I doubt it, more like the carb may still have a slight blockage. After seeing how badly the varnish had built in the sediment bowl, it wouldn't surprise me. But it runs fantastically. Haven't put it under load to see how the governor keeps up, but I could hear it kick in when my son let the clutch out in third gear.
My "test" with the clutch worked. I used the latest model clutch and pressure plate from the versions that used a pilot bearing instead of a pilot bushing. There was no problem, it adjusted up fine and feels smooth.
The steering gear is still not leaking with the NAPA 8702 and 15005 seals I put in it. Pleased with that.
For now, I'm still using the manifold we recovered off the other tractor. I haven't received the original back from the pro welder. As a result, the muffler is just sitting in the hole, not actually attached, but it is pretty tight in there so it's good enough for now.
Now to start using this tractor again. | | |
|
| |
|
| Return to Journal list |
|
What are Project Journals?
Project Journals are a place where YT Community members can document their tractor and farm projects. Each journal created, can have many photos and accompanying text entries. You can also enable comments to allow other members of the YT Community to comment on your journal. If you do enable comments, it is up to you to moderate what people enter in your journal according to the site policy of Yesterdays Tractors. Journals may also be used as photo posting area, to post your photos of your farm, tractors and related photo topics. If you would like to create a journal, just be sure you are logged in to the Classic View of the forums, and a link will appear to do so when you next come to this page. . |
Home
| Forums
Today's Featured Article -
Grain Threshing in the Early 40's - by Jerry D. Coleman. How many of you can sit there and say that you have plowed with a mule? Well I would say not many, but maybe a few. This story is about the day my Grandfather Brown (true name) decided along with my parents to purchase a new Ford tractor. It wasn't really new except to us. The year was about 1967 and my father found a good used Ford 601 tractor to use on the farm instead of "Bob", our old mule. Now my grandfather had had this mule since the mid 40's and he was getting some age on him. S
... [Read Article]
Latest Ad:
1964 I-H 140 tractor with cultivators and sidedresser. Starts and runs good. Asking 2650. CALL RON AT 502-319-1952
[More Ads]
Copyright © 1997-2025 Yesterday's Tractor Co. All Rights Reserved. Reproduction of any part of this website, including design and content, without written permission is strictly prohibited. Trade Marks and Trade Names contained and used in this Website are those of others, and are used in this Website in a descriptive sense to refer to the products of others. Use of this Web site constitutes acceptance of our User Agreement and Privacy Policy TRADEMARK DISCLAIMER: Tradenames and Trademarks referred to within Yesterday's Tractor Co. products and within the Yesterday's Tractor Co. websites are the property of their respective trademark holders. None of these trademark holders are affiliated with Yesterday's Tractor Co., our products, or our website nor are we sponsored by them. John Deere and its logos are the registered trademarks of the John Deere Corporation. Agco, Agco Allis, White, Massey Ferguson and their logos are the registered trademarks of AGCO Corporation. Case, Case-IH, Farmall, International Harvester, New Holland and their logos are registered trademarks of CNH Global N.V. Yesterday's Tractors - Antique Tractor HeadquartersWebsite Accessibility Policy |
|