Well guys, I got it done. I used a GM 4 wire alternator. 1 main output, one field input, and one turn on input, and a output for the gauge package. This came off of my 1990 buick skylark. The car was total'd about 3 years ago, breaking the alternaotr mount. I returned it for a new one since it has a lifetime warranty. Now if this one every fails, I just return it and get a new one!!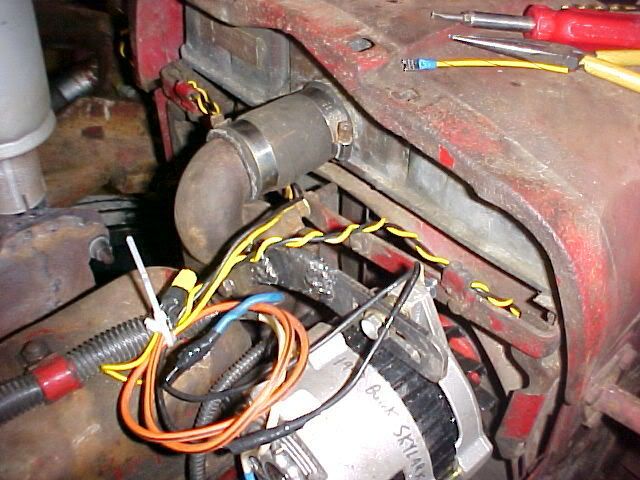
I made the mount myself. The original genny mount couldnt be used, because it bumped the pivot point too far out and would cause interference with the hood. I could have drilled a hole halfway through the mount and make the pivot there, but one of my promises to myself is to not alter original parts if I dont have to. In doing this, it keeps all part in original condition in case someone would ever need them, or want to restore the tractor. I made the top slider stepped to mount the alternator. My main pivot mount is stout as can be, and I feel it is more then adequate. It was a real pain lining it up tho, heat from welding can warp metal just enough to tick ya off!! =) If I had a wire welder I would have stitch welded it, but doing that with a stick welder is nearly impossible. Now, for the coil, I looked through the 7 my dad had laying around, and the best canditidate connection wise was a nissan coil from an old pickup. enough said. The solenoid, I wanted to address that before it became a problem. I got a ford one from advanced auto. It was a pretty close fit, but turns out not quite good enough without some modification. First, I had to flip it 180, or else the power connector on the starter would hit the frame of the solenoid. So because of that, I had to make a longer copper flat piece to bridge power from the solenoid to the starter. 
Now there is about 1" of room between the steering draglink ball end and the solenoid's "I" connector. The pic isnt very accurate from the angle. I dont see that being a problem, If I have that main cast piece break off fromt he steering box, it could hit, but then I got bigger problems then a $13 solenoid. 
I removed the regulator and bridged the few connections I needed to. 
There is a fusible link between the alternator and solenoid battery term. I also used a 1n5406 between the coil's power connection and the alterntors field and turn on terminals. 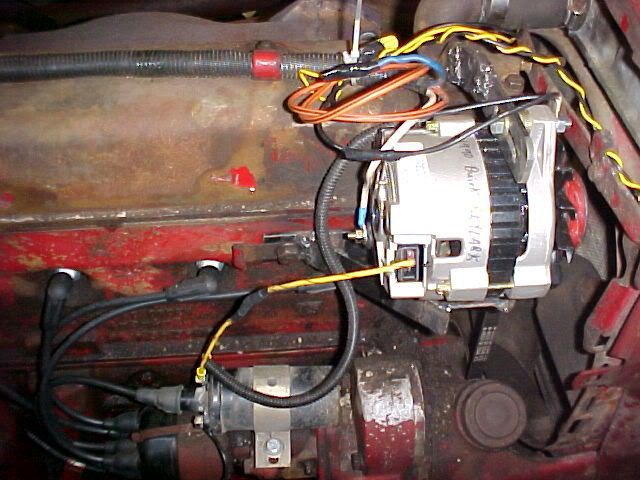
The system works great!! now for a new battery for my car, car's old battery into truck, truck battery into tractor =) Bad thing is the car and truck are side post, so I dunno if I'll get new cables or just buy a new battery soley for the tracor, or buy them stupid side to top adapters, havent decided, and for now its got a very underpowered half dead riding lawnmower battery in it. I have a 300AH battery rack in the garage I just jumper from to start it. 
The maint mount from below 
BTW, the hood does fit, the alternator has proper output voltage at engine idle speed. One thing I had to do was split a pulley because ALL of the alternator pulleys I had (about 13 of them for v belts) wouldnt accomadate my 1/2" spliceable belt. This also made the pulley smaller in diamter too =) (forgot who suggestd it on here, but thanks, nobody else had pulleys that would fit the alternator and my belt, not even the alternator/starter rebuild shop). I hacksawed it in half, then used a dremel tungsten carbide bit in the drill press to flatten out the cut edges and sandwiched a washer between them. The alternator shaft was barely long enough to get 4 turns of the nut on, so I used some loctite on the nut for added security.
Comments are appreciated...
|